Jordi Monguilod i Fornés. Protésico dental. Malgrat del Mar. Barcelona
Introducción
Horas, horas y más horas, son las que tenemos que dedicar los protésicos dentales para conseguir aquello que nos hemos propuesto, DIENTES NATURALES.
Al trabajo habitual y cotidiano, debe añadirse un continuo aprendizaje teórico y práctico motivado por las diversas técnicas y procesos de elaboración —en constante evolución—, por lo que debe agradecerse el recibir ayudas a través de artículos, estudios y aplicaciones de dichas técnicas.
Una de estas técnicas, compleja y laboriosa, es la que se refiere a las soldaduras, sometida también a constantes evoluciones, como es el conocido sistema láser y, últimamente, el novedoso procedimiento de soldadura TIG.
Rodearse de maquinaria especializada sirve, sin duda alguna, a parte de introducirnos en los nuevos tiempos, para conseguir mayor calidad, perfección y biocompatibilidad en nuestros trabajos.
De las soldaduras, deberíamos conocer tanto las propiedades y comportamientos de los materiales que vamos a utilizar como el uso de la diversa maquinaria.
Propiedades mecánicas de los metales
Sólo haremos referencia a las propiedades mecánicas de los metales, ya que son las que tenemos que tener en cuenta antes, durante y después de la manipulación de la soldadura
Las propiedades mecánicas de los metales se basan en evitar deformaciones en situaciones de carga, caracterizadas por la relación tensión-deformación (entre otras)1.
La tensión, resultante de la aplicación de una fuerza externa a un cuerpo, hace que se cree una fuerza interna igual en magnitud, pero en dirección opuesta (Figura 1).
Con toda seguridad, esta propiedad mecánica nos traerá a la mente un contratiempo común en nuestra profesión, es decir, la basculación después del colado.
Por otra parte, la deformación crea un cambio de dimensión de la estructura en cuestión. Sin embargo, esta propiedad puede ser recuperable después de retirar la fuerza aplicada, teniendo siempre en cuenta la elasticidad de los materiales.
Por lo tanto, habiendo visto estas dos definiciones, podemos constatar que son dos propiedades íntimamente relacionadas y ser observadas como ejemplo de causa-efecto:
DE LA APLICACIÓN DE UNA FUERZA EXTERNA QUE PRODUCE TENSIÓN EN UN MATERIAL RESULTA UN CAMBIO DE DIMENSIÓN O DEFORMACIÓN DEL CUERPO.
Este cambio nos indica que aparece otra propiedad a tener en cuenta, es decir, el límite elástico que representa la tensión máxima que puede soportar el material.
Estructura y propiedades de los metales
Siendo los metales una parte importante en nuestra profesión, es conveniente tener conocimientos básicos de la estructura y propiedades. Esto será de gran ayuda en el momento de comprender y solucionar futuros problemas que se nos puedan plantear en el quehacer diario.
Todas las estructuras que realizamos en prótesis son colados, es decir, el resultado de la fundición y solidificación, habiendo por tanto sufrido una modificación en la estructura molecular de dicha aleación o metal (Figuras 2A y B).
Esta estructura molecular suele ser cristalina en estado sólido. Cuando un metal o una aleación fundidos se enfrían, el proceso de solidificación se realiza a través de una cristalización y se inicia en zonas específicas, denominadas núcleos. Los núcleos suelen estar formados por impurezas en la masa fundida del metal (Figura 3 A). Los cristales crecen como dendritas, que pueden describirse como estructuras reticulares ramificadas tridimensionales y que surgen de un núcleo central (Figura 3 B). El crecimiento del cristal continúa hasta que todo el material se ha solidificado y todos los cristales dendríticos están en contacto (Figura 3 C). Cada cristal se conoce como un grano y el área entre dos granos en contacto se conoce como límites del grano1,2,5.
Después de la cristalización, los granos tienen aproximadamente las mismas dimensiones en cada dirección, medidas desde el núcleo central. No son perfectamente esféricos ni cúbicos, ni se conforman a ninguna otra formación geométrica. Se dice que tienen una estructura en grano equiaxial. Un cambio desde una estructura equiaxial a otra en que los granos tienen una estructura más larga y fibrosa puede producir cambios importantes en las propiedades mecánicas y en las posteriores manipulaciones, como son las soldaduras2.
Los límites del grano forman una barrera al movimiento molecular, por consiguiente, si aumentamos la concentración de límites con granos más pequeños, conseguiremos estructuras más estables y duras, teniendo valores mayores de límite elástico que los de estructura granular más gruesa.
Es posible obtener una estructura granular fina mediante el enfriamiento rápido después del colado.
Las estructuras existentes son:
Metales que podemos encontrar con estructura cúbica axial, serían, por ejemplo, el hierro, volframio, vanadio, metales poco dúctiles.
Con estructura cúbica con centros en las caras, encontraríamos el níquel, cobre, oro, paladio, todos ellos metales dúctiles.
![]() |
![]() |
Y por último, con estructura cúbica centrada, tenemos el titanio, cobalto, circonio (Figuras 4 A, B y C)5.
Esto, unido a factores como la composición de la aleación, su punto de fusión, el tamaño y espesor del colado, constituyen aspectos a tener en cuenta en el momento de preparar las estructuras para posteriores soldaduras, sea cual sea el sistema que se utilice.
¿Qué tenemos que saber para soldar estructuras?
Teniendo todos los conceptos claros, vemos que nos falta uno, ni más ni menos importante: ¿Qué hacer para conseguir soldar dos partes de una estructura sin que haya tensión ni modificación respecto al modelo de trabajo? Pues nada más sencillo que crear los cuatro puntos espaciales que conforman cualquier estructura estable.
Se debe tener un cuidado especial al establecer los lugares precisos donde hacer la soldadura, ya que ello reportará un punto mejor soldado y consecuentemente las uniones tendrán una mayor perfección; y, por extensión, es necesario saber que las soldaduras con soplete frente a las soldaduras con láser o sistema TIG, presentan valores de resistencia a la flexión y a la fractura mucho mas bajos2,5.
Sabiendo más sobre las estructuras, ya podemos crear estos cuatro puntos espaciales y una vez creados podemos comprobar que ya hemos unido la estructura y a la vez está estabilizada. Sólo nos faltaría puntear las zonas intermedias entre estos puntos para cerrar la estructura y evitar, de esta manera, la posible salida de gases, en el caso de que esta estructura vaya recubierta de cerámica, o pueda quedar perfectamente pulida, si ha de ser una zona libre (Figuras 5 A-L). Esto por lo que se refiere a estructuras para prótesis fija. Para estructuras esqueléticas, basta con formar un cordón de puntos de soldadura y, en el caso de que no ajustara perfectamente en el modelo de trabajo, crear varios puntos en la zona contraria a la punteada.
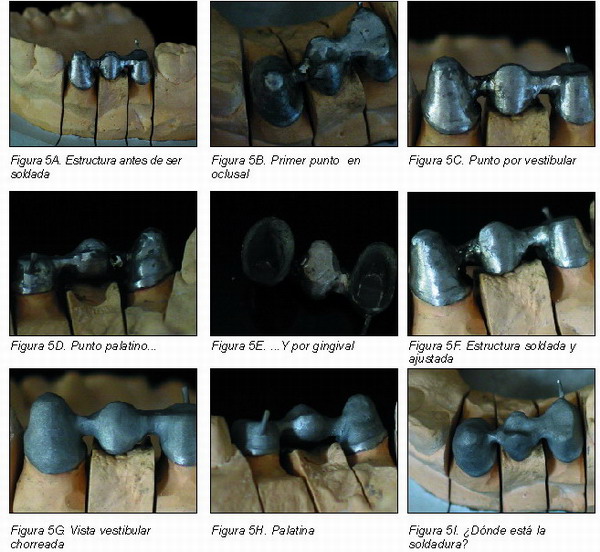
Biocompatibilidad
A lo largo de los años, se ha desarrollado un amplio y creciente número de aleaciones diferentes; por un lado, debido a las diferentes indicaciones y distintas exigencias técnicas relacionadas, y por otro, como consecuencia de las medidas de ahorro introducidas en el sistema sanitario y, por último, debido a la libre competencia. Todo esto provoca también problemas a la hora de procesar correctamente los materiales en el laboratorio, ya que deben respetarse las características específicas de cada aleación, lo que condiciona un cambio en el proceder rutinario al cambiar de aleación; esto se relaciona, así mismo, con desventajas económicas para el laboratorio protésico14,16.
Hasta no hace mucho tiempo la principal preocupación radicaba en la estética de los materiales, pero últimamente los problemas están más encaminados hacia la tolerancia de las aleaciones. Un incremento de reacciones tóxicas locales y reacciones alérgicas, todas ellas por causas electrolíticas (por contacto salival con las aleaciones), hace que se produzca una disolución de iones, y por consiguiente, una corrosión electroquímica. Dicha disolución se multiplica cuanto más materiales entren en juego. Es decir, a menor cantidad de materiales distintos usados en nuestra estructura, más biocompatible será6,14.
Esto puede inducir a que nos planteemos el uso exclusivo de los materiales clasificados como biocompatibles como son el circonio, titanio, galvano y las aleaciones de CrCo y de alto contenido en oro6,15. Además, es necesario no usar soldaduras convencionales para evitar cualquier contaminación durante el proceso de unión. En otras palabras, para unir de forma biocompatible se debe usar sistemas de pegado con composites, ya sea el sistema láser o el sistema TIG6.
Por tanto, uno de los principales aspectos que tenemos que tener en cuenta cuando decidimos escoger una aleación, radica en que tenga una buena resistencia a la corrosión. Un segundo aspecto, no menos importante, es cómo terminamos nuestra estructura protésica, ya que un acabado poroso y poco homogéneo y un pulido descuidado de partes de aleaciones metalocerámicas oxidadas y no revestidas con cerámica, pueden provocar un aumento masivo de la tasa de corrosión en estas zonas.
Concluyendo este apartado, podemos afirmar que la minimalización de componentes en las aleaciones es la meta del desarrollo moderno de las aleaciones. Se pretende incrementar con ello la biocompatibilidad y la resistencia a la corrosión, así como conseguir una optimización de las características mecánicas. También se pretende facilitar los procesos de elaboración y modelado. Se trabajará, además, en la optimización del proceso de revestimiento con cerámica o resina para aumentar así la estabilidad a largo plazo.
Con la ayuda de elementos que, o no desarrollan (por ejemplo, metales nobles) o desarrollan funciones esenciales en el organismo humano (cobalto, níquel, cromo, molibdeno, cinc y otros), se aspira a crear o seguir desarrollando aleaciones biocompatibles14.
Comparación del láser y tig ante el soplete
Para empezar a hablar de soldaduras, tendríamos que saber primero lo que significa soldar, y si cogemos un diccionario, leeremos que se trata de unir metales mediante temperatura con o sin aportación de metal.
En el momento de soldar nos podemos encontrar con dos tipos de uniones dependiendo del sistema elegido:
Unión líquido-líquido: las dos estructuras se funden en una sola, obteniéndose una interpenetración granular de los metales5.
Este tipo de unión se puede obtener mediante sistema de arco, láser, o eléctrico, entre otros.
Unión líquido-sólido: el material líquido debe tener la capacidad de adherirse al material en estado sólido. Este tipo de soldadura se obtiene básicamente utilizando el soplete, con el que conseguimos soldaduras blandas, con temperaturas entre 200 y 450 ºC, y fuertes, con temperaturas superiores.
Sabiendo esto, podemos pensar que soldar con soplete equivale a usar pegamento entre dos metales, ya que si no solapamos un material sobre otro creamos una fusión estructural20,21.
Hasta hace poco tiempo, la forma que teníamos los protésicos para unir estructuras metálicas era mediante el soplete. Creando modelos refractarios cuidadosamente preparados, pensando siempre en cómo penetraría el metal de relleno. Buscando soldaduras idóneas para cada metal sabiendo que aportábamos, entre otros materiales, cadmio, y estaño para bajar el punto de fusión; silicio que ayudaba a mejorar la fluidez, así como antioxidantes que favorecen corrosiones por electrolisis al reaccionar en la boca, y, sobre todo, haciendo que nuestra estructura no sea biocompatible por la gran cantidad de elementos en contacto. Y finalmente, jugando con las tensiones generadas por el calentamiento de grandes partes durante largo tiempo2,4,13.
Esta zona de calor, denominada ZAC, gracias a que el aporte de calor está limitado al diámetro del electrodo o del rayo tanto en el sistema TIG como en el sistema láser, permite hacer las soldaduras sin modificar las zonas próximas, ya sean zonas cerámicas o acrílicas7.
Todo esto ya nos puede hacer pensar que el tiempo empleado para la preparación hace que este sistema de soldadura no sea nada rentable para el laboratorio dental, ni por el tiempo empleado ni por los costes de los materiales.
Tampoco es rentable debido a que las aleaciones de colado modernas se han convertido en tan complejas desde el punto de vista metalúrgico, que hace que la mayor parte de los fabricantes recomienden un material de soldadura formulado específicamente, lo que nos plantea la posibilidad de la utilización de sistemas de soldadura como el láser o aparatos de sistema TIG, los cuales, a parte de permitirnos soldar directamente sobre los modelos originales, utilizamos como material de aporte la misma aleación, evitando así posibles problemas de corrosión y debilidad, es decir, creamos un trabajo biocompatible14-15.
En cualquier tipo de proceso de soldadura, la mejor soldadura que se puede obtener es aquella en la que la soldadura y el metal base comparten las mismas propiedades químicas, metalúrgicas y físicas. Para lograr esas condiciones, la soldadura fundida debe estar protegida de la atmósfera durante la operación de la soldadura mediante un aporte de gas argón, de otra forma, el oxígeno y el nitrógeno existente en la atmósfera, se combinarían con el metal fundido resultando una soldadura débil y con porosidad (Figuras 6A, B y C) 15.
¿LÁSER? Light Amplification by Stimulated Emission of Radiation (ampliación de luz por emisión estimulada de radiaciones)
Basándose en la teoría cuántica de Max Planck (1900), Albert Einstein llegó en 1917 a la conclusión de que debía existir este fenómeno y describió sus propiedades físicas, pero no fue hasta 1960 cuando Theodore Maiman construyó el primer aparato emisor de luz láser, siendo muchas las líneas de investigación que han favorecido los avances en esta tecnología. Estos avances, unidos al desarrollo paralelo de la robótica y la informática, han hecho posible la automatización de muchos procesos para facilitar su utilización en muchos campos de trabajo. El láser, debido a su alta flexibilidad (posibilidad de múltiples procesos: corte, perforado, soldadura, etc.) y la posibilidad de procesar muy diferentes materiales, se ha convertido en gran aliado de diversos sectores industriales. En el campo de la soldadura conseguimos unir numerosos materiales, ya sean iguales o diferentes entre sí, gracias a la posibilidad de determinar la intensidad y duración del impulso. Puesto que es posible concentrar el haz de láser, se pueden obtener soldaduras muy estrechas con una mínima cantidad de material fundido y poco aporte de calor, lo que disminuye al mínimo las posibles distorsiones. Así conseguimos uno de los objetivos que pretendemos alcanzar en cualquier estructura, que es un perfecto ajuste. Además se necesita emplear un gas que forme una atmósfera protectora en la zona de soldadura para obtener soldaduras limpias y libres de defectos, poros, inclusiones, etc.9,10,18.
Teniendo en cuenta la diversidad de las características de los materiales tanto como el punto de fusión y la conductibilidad térmica, es necesario aplicar una intensidad de energía diferente y específica a cada material. Para las aleaciones con una conductibilidad térmica baja, como por ejemplo las aleaciones de cromo-cobalto, se necesita menos energía que para las aleaciones de oro. Debido a esto, se plantea la cuestión de cómo debe procederse en las uniones de dos aleaciones diferentes (aleaciones de metales preciosos y CrCo). Después de diversos estudios relativos a las diferentes posiciones del centro de soldadura, se deduce que debe aplicarse más energía sobre la aleación de la que necesita. Cuando se realizan uniones de una aleación de oro con otra de CrCo hay que aplicar más energía sobre la aleación preciosa (2/3 por 1/3)17,22.
Aquí no es válida la consigna “mucho, vale mucho”, sino que lo importante es tener un conocimiento exacto de los materiales y dominar la materia. Trabajar con mucha potencia no se corresponde con las particularidades físicas. En casi todos los casos es suficiente aplicar valores de energía comprendidos en el intervalo de 30-40 W. Un aporte de energía excesivo conlleva que se produzcan reacciones indeseadas en las aleaciones y puede abocar a la destrucción de la pieza. Es decisiva la conjugación de capacidad de conducción térmica y geometría o tamaño de la restauración. Los puntos de fusión altos no conllevan necesariamente un alto rendimiento14.
¿TIG? Tungsteno Inerte Gas (procedimiento de soldadura por arco voltáico
Este proceso efectúa la unión del metal por medio del calentamiento que produce el arco voltaico. Para esto se necesitan dos terminales; por un lado, el electrodo de tungsteno y por el otro, la pieza que se va a soldar. Esta es la principal diferencia frente al láser, pues a través del electrodo creamos contacto con el objeto a soldar, mientras que con el láser se mantiene una cierta distancia. Debido a la posibilidad de determinar la intensidad y duración del impulso junto a este principio se pueden crear puntos de soldadura aún más precisos.
En la soldadura TIG, la zona de soldadura se protege de la atmósfera mediante un gas inerte que se alimenta a través de la antorcha. Este gas, el argón, se utiliza por su gran versatilidad en la mayoría de metales, además su alto rendimiento permite la realización de soldaduras con un bajo consumo de dicho gas. Dado que la atmósfera está aislada al 100 por cien en el área de soldadura y este procedimiento permite un control muy fino y preciso de la aplicación de calor (ZAC) se crean soldaduras más fuertes, dúctiles y resistentes que las realizadas con procesos al aire o con adición de soldadura externa 8,11,12.
Comparación entre el láser y el TIG
Después de describir de una manera muy superficial y llana estos dos tipos de soldadura muy semejantes para soldar nuestras estructuras protésicas, nos queda por saber, a través de estudios comparativos, si son idénticamente fiables.
En uno de estos estudios, realizado por el profesor doctor Wolfgang Lindemann, se pudo comprobar, que no sólo las soldaduras resultantes son aparentemente iguales, sino que a través del microscopio y después de diferentes pruebas de torsión, desgaste y acción química, estamos ante dos procedimientos de soldadura que no manifiestan NINGUNA DIFERENCIA SIGNIFICANTE, llevando a un idéntico resultado (Figuras 7 A y B) 23.
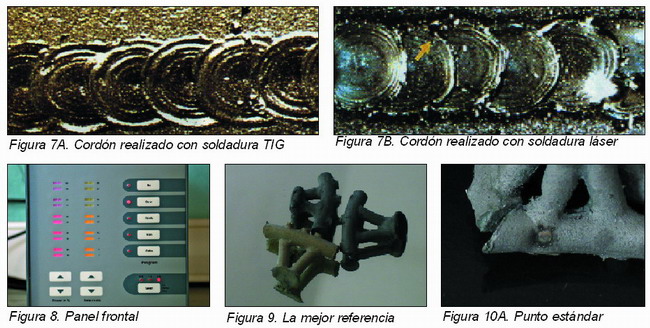
Bien. Ya sabemos que las dos técnicas son totalmente beneficiosas en todos sus aspectos técnicos.
Conozcamos el funcionamiento
Ya sabemos que, tanto el sistema láser como el TIG, regulan su función mediante la intensidad y tiempo de duración del impulso. Para facilitarnos el trabajo, la Phaser mx1 dispone de unos parámetros estándares para los principales metales con los que trabajamos diariamente (Figura 8). La intensidad (escala roja) determina la profundidad necesaria para que la estructura sea estable, y tiene que ser la justa, ni mucha ni poca. El tiempo (escala amarilla) permite variar en tamaño del punto de impacto dependiendo de la situación en que nos encontremos19.
Es cierto que, como se ha dicho anteriormente, después del colado toda aleación sufre pequeñas alteraciones, las cuales harán que adaptemos principalmente la intensidad a cada tipo de trabajo y a cada aleación. Una de las mejores y más rápida forma de adaptar la intensidad es sobre una estructura colada y, para no estropear nuestro trabajo, usar los guitos de colado (Figura 9)15.
Partiendo del parámetro estándar del metal en cuestión, punteamos una vez y comprobamos el punto que aparece (Figuras 10 A-D). Si este aparece ligeramente hundido (se aprecia gracias al estereomicroscopio incorporado), nos indica que trabajamos con cierta sobreintensidad. Bajamos un grado la intensidad y disparamos nuevamente. Si este punto entonces sale uniforme, la intensidad es perfecta. Si, por el contrario, nos aparece abultado, nos indica que falta intensidad y subimos un grado en la escala. Este proceso tiene como fin la búsqueda de la perfección de nuestra soldadura, ya que los parámetros estándares no siempre reflejan la actuación óptima.
Viendo estas fotografías, en este caso en particular, se puede apreciar que el punto predeterminado por la máquina es óptimo, ya que el segundo es más pequeño e irregular; el tercero está sobredimensionado y ligeramente hundido; y el cuarto es prácticamente inapreciable y también irregular.
En cualquier caso, tenemos que comprobar que las dos piezas a soldar están completamente limpias, ya que, en caso contrario, pueden aparecer irregularidades en la soldadura, que en un primer momento atribuiríamos a la máquina. Como remedio subimos los valores de intensidad, que sin embargo, contrariamente a lo pensado, no harían mejor la soldadura.
¿Como añadir metal a nuestras soldaduras?
Mientras nos disponemos a soldar dos estructuras, nos podemos encontrar con que:
— Se hayan modelado para tal fin. En este caso, estarán en contacto para evitar retrasos innecesarios durante el proceso de soldadura (Figuras 11 A, B y C).
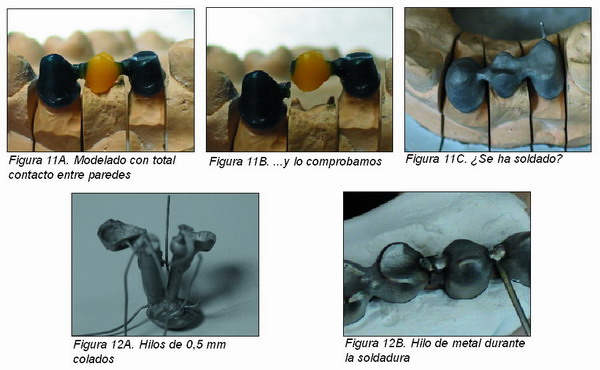
— Cortadas finamente después de ser coladas. En este caso basta con aportar metal conseguido mediante hilos de cera de 0,5 mm en nuestros colados y, por tanto, obteniendo el mismo metal que las estructuras a soldar (Figuras 12A y B) .Igual se puede adquirir hilos de aporte en varias casa comerciales.
— O tan extensas que tengamos que preparar pequeños discos, cortados del mismo guito de colado, para intercalarlos (Figuras 13A, B y C).
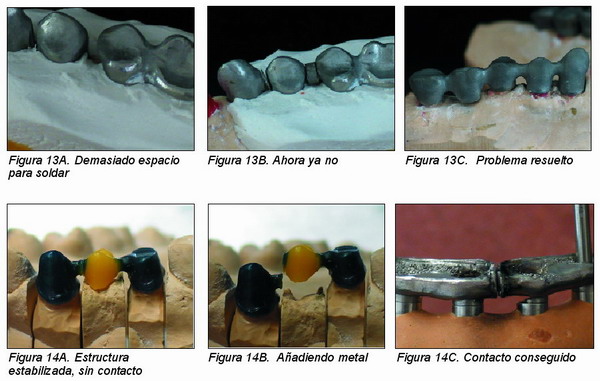
— También podemos añadir metal a una de las partes, bajando intensidad de disparo y aumentando el tiempo del mismo, con el propósito de que dé volumen a la estructura, crear contacto entre ellas, y después soldamos como se ha descrito anteriormente (Figuras 14A-E).
¿Qué hacer para eliminar tensiones?
Después de un colado pueden aparecer tensiones que hagan que la estructura colada no ajuste perfectamente en el modelo de trabajo. Pues bien, con un único impulso, sin modificar su intensidad ni tiempo, podemos hacerlo desaparecer, ya que al fundir la zona donde está concentrada dicha tensión y, como si soltáramos una goma elástica, ésta se libera y al enfriarse, vuelve a su posición original (Figuras15 A-E).
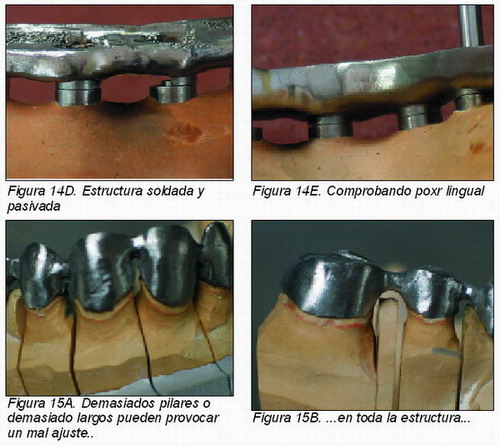
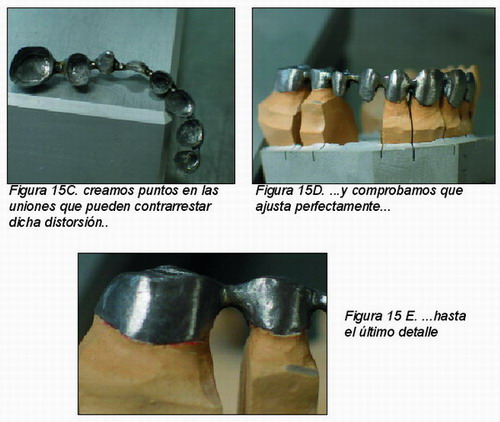
Ampliemos conectores débiles
Podría pasar, que durante el modelado en cera o durante el desbastado de la estructura metálica, debilitemos demasiado los conectores, lo que en circunstancias normales, podría plantearnos la posibilidad de volver a modelar el trabajo. Pues no, como hemos descrito anteriormente, podemos esparcir metal sobre la zona que deseemos (Figuras 16A y B).
Un sistema para cualquier eventualidad
Cámara de rechupado
Podría ocurrir, que después de preparar la estructura y chorrearla para hacer el recubrimiento cerámico, aparezcan zonas de rechupado. Podemos eliminar dichas zonas con un simple impulso aumentando el tiempo, y consiguiendo cierta difusión del metal (Figuras 17A, B y C).
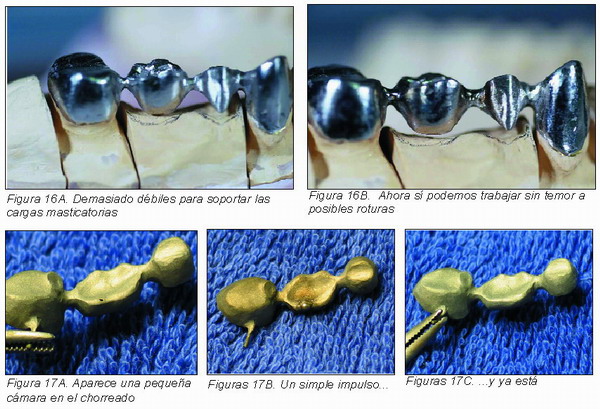
Unir puentes fracturados en boca
Nos llega al laboratorio un puente colocado en boca hace tiempo y nos preguntan si lo podemos arreglar. Sólo tenemos que tener la precaución de limpiar bien toda la estructura, por ejemplo, poniéndola en el horno de precalentamiento a unos 400 grados durante tres o cuatro horas. En este punto, ya tenemos una estructura para soldar como las que hemos descrito anteriormente (Figuras 18A-D).
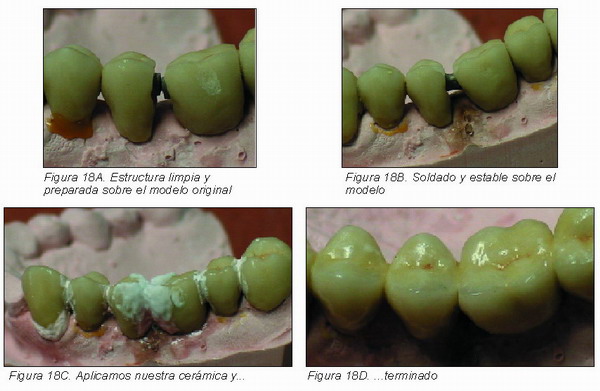
Recomposición de una estructura esquelética
También es habitual encontrar el caso de tener que añadir piezas a un armazón esquelético. Nada tan sencillo como modelar la estructura necesaria y soldar sobre el modelo (Figuras 19A, B y C).
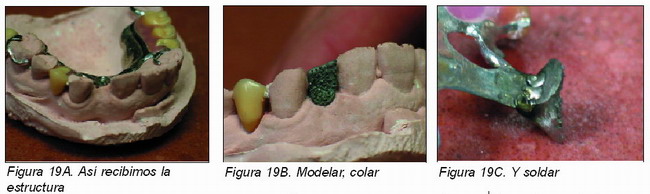
Se ha perforado una estructura
A veces, debido a un mal calibrado, un insuficiente espacio de la preparación o un descuido, la estructura puede perforarse. Esto nos obliga a volver a modelar la estructura con la consiguiente pérdida de tiempo y materiales, sin contar con la desorganización de trabajo.
Pues bien, con un poco de práctica y conocedores de los parámetros explicados se puede reparar la perforación en cuestión de minutos (Figuras 20A-D).
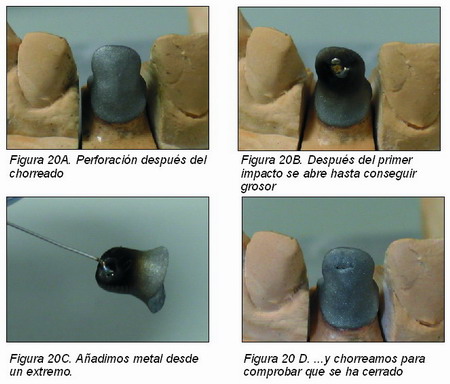
¿Qué hay que hacer para soldar distintos metales?
Para soldar diferentes metales, como nos podemos encontrar en un trabajo combinado de anclajes y estructura esquelética, siendo conocedores ya de todos los conceptos y parámetros necesarios para cualquier eventualidad, sólo nos falta recordar que, debido a la diferencia de estructuras moleculares y de composición, debemos trabajar sobre el metal con punto de fusión más bajo. Es decir, si tenemos una situación de oro y cromo-cobalto, trabajaremos sobre el oro para que se funda sobre el cobalto, ya que si lo hacemos al revés, por diferencias de punto de fusión y por falta de intensidad, el cromo-cobalto se adaptará sobre el oro sin llegar a fundirse con él22.
Por todo lo descrito, nos encontramos ante un sistema que, a parte de rapidez, permite uniones fiables, seguras y biocompatibles. Es decir, podemos hacer lo que nos propongamos, siempre que conozcamos los conceptos y tengamos un poco de paciencia porque, como dijo en su día Leonardo da Vinci: “Aquellos que trabajan sin método ni fundamento, son como pilotos que navegan sin brújula ni compás y nunca saben con certeza a dónde van“.
No nacemos sabios, estamos en constante aprendizaje, y esto nos traerá la satisfacción de ver nuestro trabajo bien hecho.
Conclusión
Por todo lo mostrado y a través de la experiencia personal, sólo queda decir que este nuevo método para realizar las soldaduras ha contribuido en mi quehacer diario no sólo a solucionar problemas ahorrando tiempo y materiales, sino también y lo que es más importante, a conseguir trabajos de una mayor calidad estructural y de una biocompatibilidad extrema.
También me ha traído tranquilidad; una tranquilidad traducida en el hecho de no pensar en posibles problemas que pudieran surgir después de un colado o de una prueba de metal o de una compostura metálica, ya que todos estos casos se han podido solucionar en cuestión de minutos de forma fiable y segura.
Permitir que las nuevas tecnologías entren en nuestros laboratorios, sin lugar a duda, nos facilita el trabajo, nos hace más competitivos y, lo que es más importante, nos da más tiempo para dedicarnos a la creación artística de nuestro trabajo, el diente.
A través de este artículo se intenta aproximar al profesional los avances tecnológicos que pueden hacer el trabajo cotidiano mucho más fácil, cómodo y, sobre todo, con resultados altamente satisfactorios.
No discutir si el láser o el TIG es mejor, pues esto quedará para la interpretación de cada profesional.
Correspondencia
Jordi Monguilod i Fornés
St. Antoni de Padua, 3
08380 – Malgrat de Mar (Barcelona)
artdent@copdec.es. G
Bibliografía
1. McCabe JF, BSc, PH.D,M.R.S.C, Chem C. Anderson-materiales de aplicación dental. Salvat Editores, SA.
2. Fischer J. Estética y prótesis. Consideraciones interdisciplinarias. Ediciones Latinoamericanas.
3. Spiekermann H. Atlas de Implantología. Masson.
4. Rosentiel SF, Land MF, Fujimoto J. Prótesis fija: procedimientos de clínica y de laboratorio. Salvat Editores, S.A.
5. López-Álvarez JL. Técnicas de laboratorio en prótesis fija.
6. Prof. Dr. Edwin Lenz. Titan als werkstoff für kombiniert festsitzenden und abnehmbarem zahnersatz. Universidad Jena/Erfurt, Alemania, 1989, Spitta Verlag.
7. Rodríguez Salgado D. Soldadura. Tecnología y técnica de los procesos de soldadura. Bellisco, Ediciones Técnicas y Científicas.
8. www.drweld.com.
9. www.avilam.com.
10. www.jorge-alonso.com.
11. www.geocites.com.
12. www.monografias.com.
13. Quintessence Técnica. 4/98 abril. Vol 9, n.º 4, pp. 235-239.
14. Quintessence Técnica. 7/98 agosto/septiembre. vol 9, nº 7, pp.393-397, pp.410-412.
15. Quintessence Técnica. 1/2000 enero. Vol 11, nº 1, pp.57-62.
16. Quintessence Técnica. 10/2000 diciembre. vol 11, nº 10, pp. 573-587.
17. Soproden. vol. Xlll, nº 3, 1997, pp.175-183.
18. Soproden. vol. Xll, nº 6, 1996, pp. 431-433..
19. Soproden. vol. Xl, nº2, 1995, pp.137-140..
20. Labor Dental. Vol. 1, nº 1, noviembre 1998, pp. 74-79.
21. Labor Dental. Vol. 1, nº 2, diciembre 1998, pp. 125-134.
22. Labor Dental. Vol. 3, nº 4, abril 2000, pp. 248-251.
23. Labor Dental. vol. 7, nº 6, junio-julio 2004, pp. 376-381.