José Cruz Martín Pozo. Técnico de Laboratorio de Prótesis Dental. Director de centro de formación en prótesis. Madrid
Resumen
Estudio comparativo de los dos sistemas más extendidos para la realización de muñones individuales: Pins y Bases de plástico.
Análisis, tanto desde el punto de vista de economía de tiempos, materiales, maquinaria, etc, como de precisión y facilidad de realización.
Abstract
Comparative study of fabrication systems of saw-cut dies: “Pin” and Tray-models. Analysis: time-saving time, materials- saving, needless equipement. Precise and ease elaboration.
Palabras clave
Muñones individualizados o desmontables, “pins”, base plástico para individualización, exactitud.
Key words
Individualized or detachable dental dies, pins, tray models, precision.
Introducción
A lo largo de los años, primero como protésico y después como educador, siempre he estado rodeado de la polémica sobre qué sistema de individualización era mejor: los pins o las bases plásticas. La experiencia me ha dado la respuesta: “depende de qué “pin” y depende de qué base”.
Me explico:
Lo primero que debemos pedirle a un sistema de individualización es que sea preciso, es decir, que después del corte del modelo los muñones y/o las piezas, se mantenga con total exactitud su relación inicial.
Lo segundo es que sea sencillo, que no necesite de complicados aditamentos, accesorios o maquinarias especiales para realizarlo.
En tercer lugar, que sea rápido; el mercado no nos permite perder tiempo en preparar un modelo, tiempo que necesitamos para realizar realmente la prótesis.
Y por último, que el sistema no nos estorbe en el momento de trabajar con el modelo, o de montarlo en el articulador, o incluso a la hora de enviarlo a clínica.
Exigencias a los “pins”
Dentro de los “pins” siempre debemos optar por aquellos que lleven la “camisa” metálica (en algunos casos son aceptables las camisas plásticas), no son admisibles los que sin “camisa” confían el ajuste sólo a la escayola de la base; deben de tener un sistema de posicionamiento que, por sí mismo, impida la movilidad rotacional del elemento individualizado; las muescas o huellas en la escayola no son, hoy en día, admisibles dada la inexactitud que han demostrado. Por otro lado deben de ser lo más estrechos posibles para poder adaptarse a piezas con muy poca dimensión interproximal sin debilitar las paredes de escayola que los soportan.
Exigencias a las bases de individualización
En el caso de las bases plásticas debemos exigir lo primero lo mismo que a los sistemas de “pins”: precisión. Las partes individualizadas deben de permanecer firmemente ancladas en su posición sin ninguna variación de posición respecto del modelo entero. Esto normalmente se consigue con varios parámetros a tener en cuenta: un plástico de primera calidad, lo suficientemente rígido y bien dimensionado en cuanto a su estructura, que no permita ningún tipo de oscilación.
Una acanaladura interna que, permitiendo el deslizamiento suave del modelo, sea lo suficientemente larga (alta) para evitar los balanceos de la pieza individualizada y con un espacio mínimo entre estrías para que todas las piezas, incluso las muy finas, tengan siempre una referencia y retención posicional.
Asimismo debe ser un sistema sencillo, sin elementos de retención o montaje complicados, con los menos elementos móviles o de ajuste, que no precise de maquinaria o instrumentos para la elaboración del modelo, su individualización o manejo.
También es preciso que sea rápido, que no nos demore el poder empezar con el trabajo de realización de la prótesis.
E igualmente como última condición, que sus dimensiones o diseño no nos “complique” el trabajo, tanto a la hora de la manipulación del modelo como, por ejemplo, montarlo en articulador.
Una vez establecidos los principios de las cualidades que deben reunir cualquiera de los dos sistemas, la pregunta seguía en el aire: pins o bases. La única forma de contestarla era realizar trabajos idénticos con ambos sistemas y comparar parámetros.
Establecimiento de requisitos
Lo primero que teníamos que pedir a los dos sistemas era que fueran precisos. Por razones que todos comprendemos, este era el último punto que podríamos comprobar, al acabar de realizar los modelos de prueba. Por tanto elegiríamos unos sistemas que ya llevamos tiempo utilizando, tanto para el trabajo real de laboratorio como para los trabajos en el Centro de Formación, y que por sus resultados podíamos considerar “a priori” como fiables, solo a falta de la comparativa final.
Para analizar los demás parámetros (sencillo, rápido y manejable, ) lo mejor era realizar y analizar paso a paso el sistema de realización de cada uno y después establecer las diferencias.
A los anteriores requisitos, pensé en añadirle otro: el “económico”, íntimamente ligado a los anteriores, pero muy importante para la rentabilidad del trabajo y que muchas veces no se valora convenientemente.
Método de realización y parámetros para la comparativa
El sistema seguido ha sido la realización de modelos individualizados, de un mismo modelo (impresión) y tres veces con cada sistema. La metodología seguida estrictamente es la descrita en el presente artículo. Con cronometraje de tiempos en cada fase, siendo el tiempo mostrado la media de los tiempos obtenidos en cada una de las tres repeticiones de cada caso. He de hacer hincapié en que se ha evitado el “hacer carreras”, o en utilizar “atajos” o “trucos” para acelerar el trabajo. La manipulación de los materiales o modelos ha sido siempre siguiendo las normas de obligado cumplimiento, y si bien se ha empleado siempre la máxima rapidez que conceden treinta años de profesión, ha primado la consecución de un trabajo de calidad, con la exigencia adecuada a un trabajo cotidiano de laboratorio.
Asimismo, se detallan la maquinaria utilizada, útiles específicos (no los de uso común) y los materiales cuyo coste pudieran tener alguna repercusión en la comparativa de la economía de los sistemas.
A continuación se describen pormenorizadamente las fases realizadas, con los parámetros de tiempo y maquinaria utilizados en cada una de ellas.
Modelo elegido:
• Piezas talladas: – – – – 13 12 11 21 22 – – – – – – -26
• Piezas sin tallar: – – – – – – – -14 – – – – – – – – – – – – – – – – – – – – -27
• Zonas edéntulas: (17 16 15) – – – – – – – – – – – – – (23 24 25)
Tramos a individualizar: [17 16 15] + [14] + [13] + [12] + [11] + [21] + [22] + [23 24 25] + [26] + [27]
Modelo individualizado con “pins”
Pins de una sola espiga, con camisa y sistema antirrotatorio (Figura 1).
Fases a realizar
1) Preparación de la impresión
Limpieza, recorte del material que sobresale de la cubeta y aplicación de spray para eliminación de tensiones y preparación de la superficie de la silicona para mejorar el deslizamiento de la escayola sobre ella (Figura 2).
Tiempo empleado: 0’ 30’’.
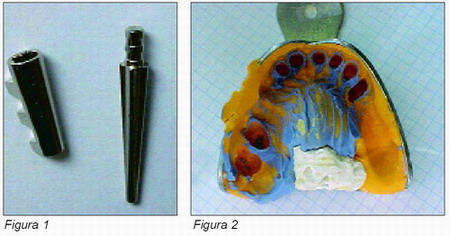
2) Preparación de la escayola
La escayola a utilizar. Clase IV, debe de ser pesada y medida el agua, para asegurar una correcta expansión y conservación de las cualidades físicas de la escayola (Figura 3).
Tiempo empleado: 0’ 30’’
Material empleado: 100 gr. de escayola clase IV.
3) Mezcla y batido de la escayola
Una vez ”ligada” la escayola con el agua, se termina la mezcla al vacío (Figura 4).
Tiempo empleado: 1’ 22’’.
Maquinaria: mezcladora al vacío.
4) Vaciado de la impresión
Con el empleo de un vibrador, se “vacía” la impresión, con la escayola preparada, lógicamente prestando especial atención a NO atrapar burbujas de aire en las piezas o muñones de la preparación (Figura 5).
Tiempo empleado: 1’ 18’’.
Material: 100 grs. de escayola Clase IV.
Maquinaria: Vibrador.
Una vez cubiertas las piezas y partes importantes de la impresión dejamos de vibrar, terminando de cubrir la zona de la arcada dentaria, dándole el suficiente espesor para que no se nos rompa al “sacar” el modelo de la cubeta.
Tratamos de no cubrir la parte central (palatina) en los modelos superiores, puesto que como posteriormente tenemos que eliminar esa zona, el trabajo nos resultará más cómodo.
Tiempo empleado: 0’ 13’’.
Tiempo fraguado modelo : 35’ 00’’.
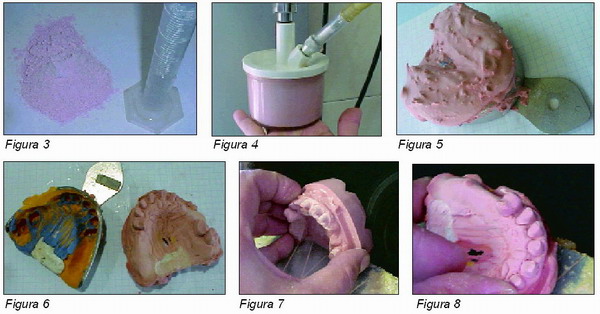
5) Aplanado y recorte del modelo
Una vez transcurrido el tiempo de fraguado inicial de la escayola (de 20 a 45 minutos según fabricantes) se extrae el modelo de la impresión (con el máximo cuidado de no fracturar las piezas o muñones) (Figura 6).
Ahora hay que preparar el modelo para posicionar los “pins”.
Primero se recorta la base para dejarla lo más plana y lisa posible, es preferible la utilización de una recortadora en seco, aunque puede utilizarse una recortadora en húmedo siempre y cuando no se “empape” el modelo y el aporte de agua sea mínimo para no variar la expansión de la escayola (tengamos en cuenta que el proceso de fraguado y expansión de la misma no acaba hasta transcurridas al menos 24 horas) (Figura 7).
Aparte de recortar la parte inferior del modelo conviene también eliminar las partes más “gruesas” de los bordes laterales, prestando especial atención a la estabilidad del modelo, pues si éste se nos escapara es muy posible que se nos “desbastaran” piezas, muñones o partes importantes del modelo, obligándonos a repetir todo el proceso de vaciado (Figura 8).
Tiempo empleado: 01’ 54’.’
Maquinaria: recortadora en seco o en húmedo.
A continuación se procede al recortado de la parte interior.
Para esta tarea lo ideal es contar con una recortadora de interiores cuya fresa nos da una superficie lisa, uniforme y con una conicidad adecuada para referenciarnos posteriormente los pins con respecto a la base del modelo (Figuras 9, 10 y 11).
Se puede usar en este proceso el micro-motor con una fresa adecuada para desbastar escayola, aunque las superficies obtenidas ni serán lisas ni homogéneas ni con la conicidad adecuada para dejar una base correcta (Figura 12).
Tiempo empleado: 01’ 42’’ (con micromotor: 03’ 33’’).
Maquinaria: Recortadora en seco o en húmedo.
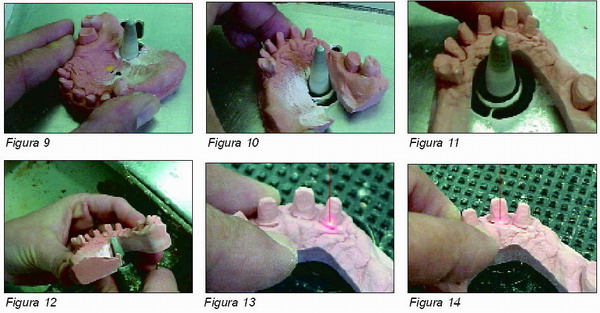
6) Perforaciones para los pins
Una vez obtenida la “herradura” de nuestra arcada dentaria procedemos a realizar las perforaciones para los pins.
Este trabajo se ha de realizar siempre con una perforadora para pins a fin de conseguir dos objetivos: el que estos vayan correctamente posicionados y que a la vez estén perpendiculares entre sí, para permitir una extracción de los muñones una vez individualizados (Figuras 13 y 14). Nunca se deben realizar “a mano” pues ni existe paralelismo ni se consigue un ajuste exacto de la cabeza del pins en el orificio, siendo mucho más fácil su despegado o fractura de la escayola (Figura 15).
De esta forma se obtienen unas perforaciones perfectamente adaptadas a la cabeza de los pins, posicionadas correctamente y con el suficiente espesor de escayola alrededor del orificio para evitar futuras fracturas de las paredes de escayola que sujetan dichas cabezas (Figuras 16 y 17).
Tiempo empleado: mínimo 00’ 11’’ (1 perforación) + 00’ 06’’/perforación de más.
En este caso: 10 perforaciones = 00’ 11’’+ (9 X 06’’)= 01’ 05’’.
Maquinaria: perforadora para pins.
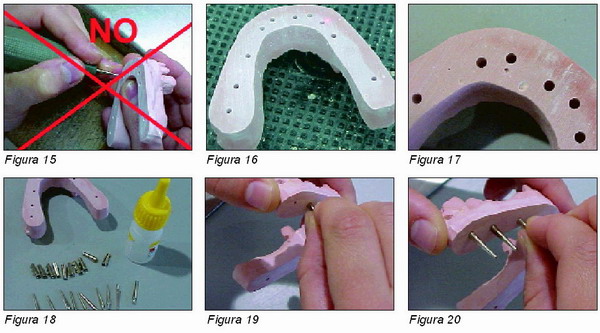
7) Fijación de los “pins”
Preparamos el modelo, los pins que vayamos a emplear y el pegamento de cianocrilato para fijarlos en su sitio. (Otros sistemas permiten el atornillamiento de los pins, pero cuando éstos no son cilíndricos tal sistema no es posible, aparte de que es mucho más delicado el no romper las paredes de escayola.)
Comprobamos que los pins “entran” en todos los agujeros, sin holgura pero sin excesiva presión (Figuras 18, 19 y 20).
El método más seguro para que no nos sobre ni nos falte pegamento en cada cabeza de los “pins” es verter unas gotas del pegamento en un recipiente pequeño (Figura 21), en el que sumergimos dicha cabeza, quedando en ésta una gota, la cantidad adecuada para pegar, sin exceso ni carencias, cada elemento (Figuras 22, 23, 24 y 25).
Una vez posicionados todos los pins, se cubren las puntas de los mismos con cera, o con un aditamento plástico en otros modelos de pins, para facilitar su posterior localización en la base del modelo (Figuras 26 y 27).
Tiempo de realización: mínimo 01’ 15’’ + 00’ 14’’ minuto/pins (con colocación de testigos).
En este caso: 01’ 15’’ + (10 X 14’’) = 03’ 35’’.
Tiempo de espera para asegurar una correcta adhesión y no llevarnos sorpresas después por desprendimiento de los pins: 05’ 00’’.
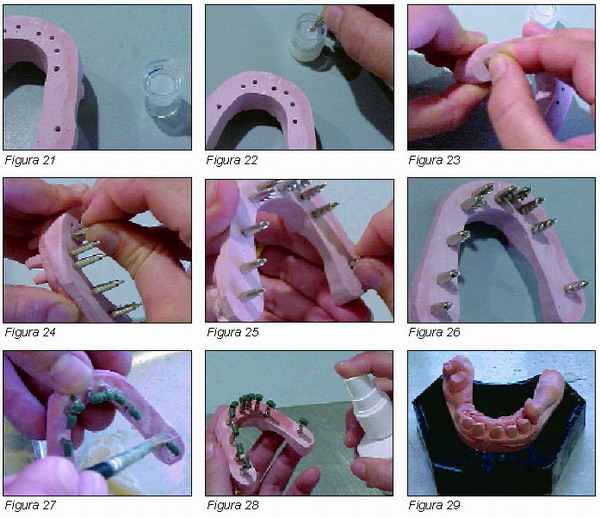
8) Realización de la base-soporte
Posicionamos la herradura en un zocalador para facilitar la formación de la base del modelo. Previamente la hemos de tratar para evitar la adhesión entre las capas de escayola. Este aislante debe de reunir las cualidades de no crear capas y permitir una fácil separación. La escayola utilizada debe ser la misma que el modelo y con la misma proporción, igualando así las expansiones y características de ambas (Figuras 28 a 32).
En este paso podemos incluir un elemento de retención para montaje en articulador.
Tiempo empleado: 03’ 15’’ (incluyendo preparación y mezcla de escayola).
Material:
• 150 grs. de escayola clase IV (para un conformador de base estándar y pins cortos).
• Aislante escayola-escayola.
Maquinaria:
• Mezcladora al vacío.
• Vibrador.
• Zocalador.
• Elemento retención montaje.
Esperamos el tiempo necesario para un correcto fraguado (endurecido) inicial de la escayola
Tiempo de fraguado: 35’ 00’’.
Una vez transcurrido dicho plazo, podemos desmoldar el modelo (Figuras 33 y 34).
9) Recorte de la base-soporte
Procediendo al recortado del modelo, tanto del sobrante alrededor como de la base del mismo hasta “intuir” la cera o marcadores que habíamos posicionado en el extremo de los pins (Figuras 35 a 37).
Tiempo de realización: 00’ 57’’.
Maquinaria: recortadora en seco o en humeado.
10) Separación de arco dentario y base
Con el fin de no dañar los extremos de los pins, no se debe llegar con la recortadora hasta éstos, sino que con un instrumento se descubren dichos extremos. Y empujando leve y alternativamente la herradura se desplaza y se separa de la base con total suavidad (Figuras 38 a 41).
Tiempo de realización: 00’ 52’’.
Elaboración de modelo Individualizado con “base de plástico”
Base de plástico de un solo cuerpo, con fijaciones laterales incrustadas al modelo (Figuras 42 y 43).
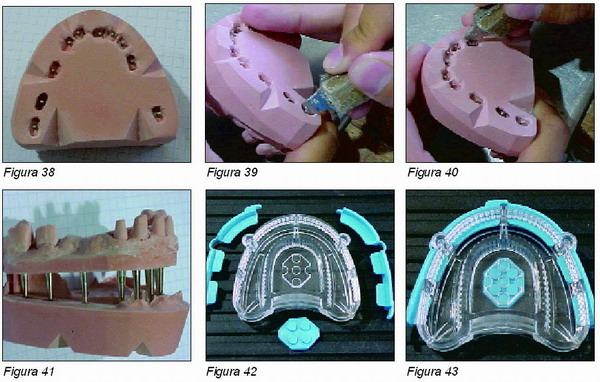
1. Preparación de la impresión
Limpieza y recorte del material que sobresale de la cubeta: si la extensión de la impresión lo permite, es conveniente cortar a borde del límite metálico de la misma. Y, si es factible, cortar la parte más elevada del paladar para tratar de dejar un plano al mismo nivel.
Sobreponemos la cubeta a la impresión y vemos, debido a la transparencia de aquélla, posicionamos cómoda y perfectamente los elementos a individualizar en la zona correspondiente al arco ranurado (Figuras 44 y 45).
En esa posición realizamos un marcas que nos referencian ambos elementos (Figuras 46 a 48).
Aplicamos el spray para eliminación de tensiones y preparación de la superficie de la silicona para mejorar el deslizamiento de la escayola sobre ella. NO es necesario dar ningún tipo de aislante o separador en la base de plástico, puesto que su superficie pulida a alto brillo, no efectúa ningún tipo de agarre o retención sobre la escayola.
Tiempo empleado: 00’ 57’’.
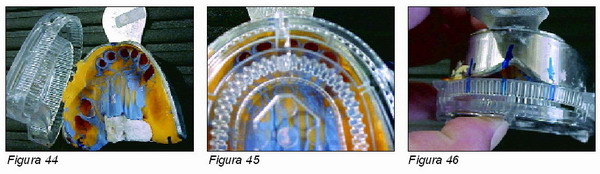
2. Preparación de la escayola
La preparación de la escayola se realiza igual que para el sistema de “pins”. Preparando mayor cantidad, pues vamos a vaciar la impresión y la cubeta a la vez (Figura 3).
Tiempo empleado: 0’ 30’’.
Material empleado; 150 gr. de escayola clase IV.
3. Mezcla y batido de la escayola
Seguimos las mismas pautas que para el mezclado de cualquier clase de impresión para prótesis fija (Figura 4).
Tiempo empleado: 1’ 22’’.
Maquinaria: Mezcladora al vacío.
4. Vaciado de la impresión
Positivamos la impresión, superando muy levemente con la escayola los bordes que hemos definido con el recorte de la silicona, prestamos atención al correcto “llenado” de las piezas y muñones, para evitar cualquier clase de burbuja o falta de llenado del molde. Si se utiliza el vibrador este sólo debe estar en funcionamiento mientras se vierte la escayola, nunca dejar la impresión vibrando después, pues se pueden formar más burbujas por agrupamiento espontáneo de micro-burbujas dentro de la mezcla.
Con la misma mezcla se llena, enrasándola también, la cubeta, unos golpecitos bastan para una correcta distribución de la escayola por el interior de la misma, aunque también se le puede someter a una muy breve vibración (Figura 49).
Tiempo empleado: 1’ 29’’.
Maquinaria: vibrador.
5. Unión de arco dentario y base
Cuando la escayola obtiene una cierta consistencia no fluida (dependiendo de la escayola usada esta consistencia puede alcanzarse cuando se termina de llenar la cubeta) y todavía sin comenzar el ”endurecido” de la masa, se posiciona la base sobre la impresión haciendo coincidir las marcas que con anterioridad habíamos realizado (Figuras 50 a 52).
Y dejamos apoyado el conjunto SOBRE LA BASE, hasta el fraguado de trabajo de la escayola (Figura 53).
Tiempo empleado: 00’ 12’’.
Tiempo de fraguado: 35’ 00’’.
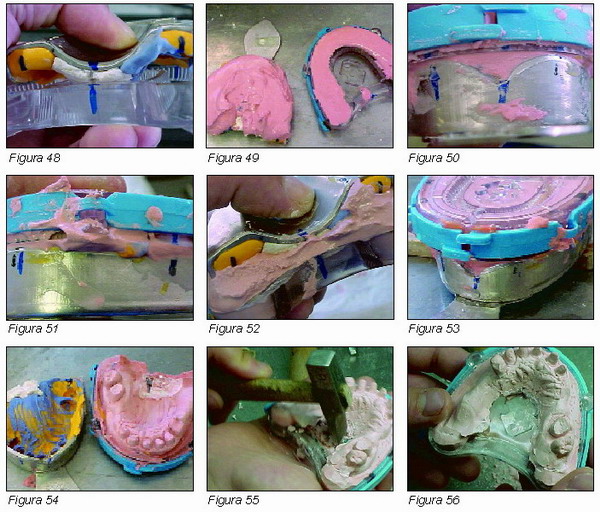
6. Extracción…
Transcurrido el tiempo de fraguado de la escayola (de 20 a 45 minutos) se puede proceder a extraer el modelo de la impresión.
Si se ha sido sólo un poco cuidadoso, se obtiene un modelo libre de rebabas o restos de escayola alrededor de la base, lo cual nos va a ahorrar tiempo en los pasos siguientes (Figura 54).
Antes de sacar el modelo de la cubeta, golpeamos ligeramente con un martillito sobre la zona correspondiente al nervio interno de la base; de esta forma, si se nos hubiera metido escayola en la escotadura central, ésta se quebrará a nivel de este nervio, facilitándonos el posterior recorte de las rebabas de escayola (Figuras 55 y 56).
Procedemos a retirar las fijaciones laterales con un cuchillo se realiza una suave palanca entre éstas y la base, retirándose con facilidad (Figuras 57 y 58).
A continuación, con unos golpecitos alternativos en los resaltes de la base a nivel de canino y en la parte posterior, el modelo es fácilmente desmoldado (Figuras 59 a 63).
Gracias a las nítidas y pulidas formas internas de la base, el modelo reproduce exactamente el interior de la base, permitiendo el ajuste máximo del modelo sobre la misma.
Tiempo empleado: 00’ 54’’.

… y recorte del modelo
Sólo nos queda recortar las zonas sobrantes de escayola.
La parte interna, casi exclusivamente en los superiores, se elimina fácilmente gracias al ángulo afilado interno que presenta la base, y por los golpes que antes de sacarle de la base le habíamos dado.
Los excesos externos y los restos internos se eliminan con una fresa de escayola, dejando la herradura dentaria a ras de la superficie interna de las paredes de la base (Figuras 64 y 65).
Y ya tenemos el modelo listo para individualizar y preparar los muñones.
Tiempo de realización: 01’ 29’’.
Maquinaria utilizada: micromotor.
En este punto hemos llegado a tener realizado el 80 por ciento del trabajo de la comparativa de los dos sistemas.
Tenemos las seis herraduras dentarias (tres con cada sistema) dispuestas para ser cortadas en los tramos previstos (Figura 66).
Análisis a la primera parte del estudio
Hasta aquí podemos comparar: TIEMPO, MATERIALES Y MAQUINARIA para cada uno de los dos sistemas, quedándonos pendiente el ajuste de cada uno de ellos. Para no hacer demasiado largo este artículo, realizamos una primera tabla comparativa y en un artículo posterior analizaremos tanto la precisión de los mismos como la forma más conveniente de cortar y preparar los muñones para la realización correcta de nuestro trabajo.
Tabla comparativa de TIEMPO–MATERIALES–MAQUINARIA (Explicación):
Para una mejor cuantificación de los procesos, pasamos los datos obtenidos a una tabla comparativa.
En el centro describimos las fases realizadas, unas son comunes y otras sólo de un sistema. A cada fase ponemos el tiempo empleado, los materiales usados y la maquinaria o útiles específicos utilizados.
Los datos obtenidos los simplificamos y unificamos en una segunda Tabla Resumen.
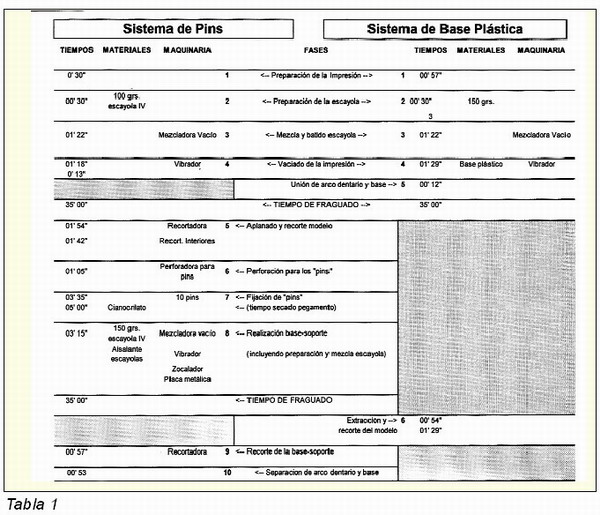
Los tiempos se unifican en: tiempo de manipulación y en tiempos de espera de fraguado o secado de materiales.
La suma de ambos nos da un tiempo total para la elaboración del modelo.
En dos apartados siguientes se recogen los materiales, maquinaria y útiles específicos, se enumeran y en caso necesario se pone la cantidad usada.
Y por último queda la valoración de los datos. Para ello, puntuamos de la siguiente manera:
Se le da un punto positivo según las medidas siguientes:
Menor tiempo de realización (tiempo manipulado y tiempo de espera).
NO utilización o empleo de menor cantidad de material.
NO empleo de maquinaria o útiles.
En caso contrario se puntúa con 0. Y se suman las puntuaciones corres-pondiente a cada sistema.
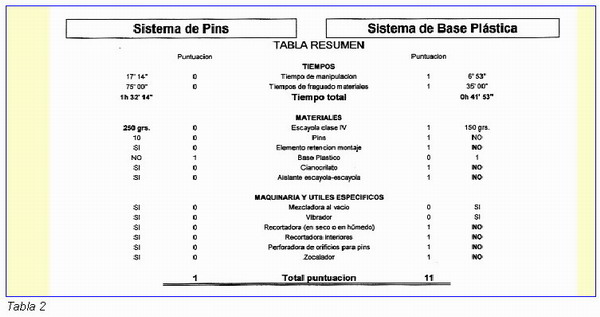
Conclusiones de la primera parte del estudio
Una vez estudiado el resultado, este no puede ser más concluyente: 11 puntos a favor del sistema de bases plásticas – 1 punto el sistema de pins.
Objetivamente, podemos considerar que, por ahorro de tiempo, ahorro de materiales, ahorro en inversiones de maquinaria, ahorro de fases y sencillez de manejo, la opción del sistema de bases supera ampliamente a los sistemas de pins.
Nos queda por analizar la seguridad de la precisión y la manejabilidad de los modelos, que como ya adelantábamos al principio del artículo queda para exponerlo en una segunda parte, que desarrollaremos en un próximo artículo. En él, además de analizar los valores mencionados, trataremos de ver también las posibles opciones, como por ejemplo la individualización de modelos que se reciben de clínica ya vaciados o la utilización en casos de implantes.
Correspondencia
José-Cruz Martín Pozo
Centro de Formación DE LAS CASAS
C/ Eraso, 36, 3ª plta.
28028 MADRID
dlcasas@formaciondental.com v