Resumen
Contando con las nuevas tecnologías CAD-CAM introducidas en el desarrollo de nuestro proceso de trabajo diario, llegamos a materiales blancos de alta dureza, imposibles de colar, químicamente inertes como el ZIRCONIO.
Diseño de híbridas con perfecto ajuste pasivo y fresados en titanio, evitando alteraciones en sus propiedades, diseñando todo tipo de fresados curvos con más de un póntico.
Palabras clave
CAD-CAM, escaneado, fresado, zirconio, titanio, cerámica, estética.
Key words
CAD-CAM, scanned, mechanized, zirconio, titanium, ceramics, aesthetics.
Summary
Using the new technologies CAD-CAM got in the development of our process of daily work, we get to white materials of high hardness, impossible to fuse, chemically passive as the ZIRCONIO. The design of hybrid with perfect passive adjustment and mechanized in titanium avoiding alterations in its properties, designing all kinds of mechanized curved with more than one intermediate piece.
Introducción
El mundo tecnológico que nos rodea a veces llega a superar lo inimaginable por la mente humana. Hoy en día con las nuevas tecnologías que nos ofrece la prótesis conseguimos realizar trabajos estéticamente perfectos, con materiales que con una maquinaria altamente tecnológica y la mano de un profesional conseguimos dar forma a trabajos de máxima estética.
Trabajando todos estos años, buscando materiales que se asemejen a un metal convencional en dureza; tratando de buscar ajustes precisos en colados curvos y realizar puentes de más de un póntico; químicamente inertes; evitando los posibles cambios en las propiedades físico-químicas por una mala manipulación, llegamos a diseños fresados en titanio y materiales de alta dureza como el zirconio (biocompatibles con el cuerpo humano).
Nuevos sistemas informáticos que evolucionan continuamente adaptándose a las exigencias del técnico, regenerando software de nueva generación que dan forma a estos materiales. Sistemas altamente complejos y precisos asistidos por ordenador: CAD-CAM. El sistema escogido por el centro de fresado Ortodentis está compuesto por un escáner (DCS Preciscan), un software (DCS Denform) y una fresadora (DCS Precimill).
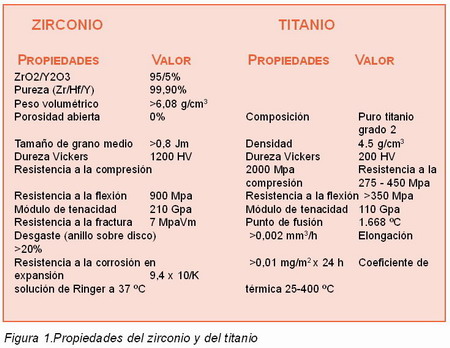
Desarrollo
Para la realización de trabajos implantosoportados se debe partir siempre de modelos de trabajo que reproduzcan fielmente la posición de los implantes en boca, utilizando para ello la técnica FRI (férula rígida de impresión). Esta es muy exacta, ya que cada aditamento para impresiones es ferulizado circunferencial, simétrica e individualmente en boca con escayola mediante una estructura rígida metálica. Se arrastrará con un material de impresión preciso y una cubeta individual fenestrada (técnica publicada en el libro Rehabilitación oral en prótesis sobre implantes del Dr. Vicente Jiménez López).
Antes del diseño sobre el modelo original mandaremos un montaje en dientes donde verificamos y adquirimos las referencias ideales para el desarrollo de la estructura final.
Una vez preparado el modelo original, colocaremos sobre los implantes los pilares manofacturados de titanio, paralelizándolos con la microfresadora, creando un eje de inserción correcto para el futuro escaneado.
Recibidas las impresiones originales en el laboratorio, las vaciaremos con escayolas específicas de expansión cero, prepararemos el modelo con cualquier sistema de individualización y volveremos a vaciar las mismas impresiones diseñando un modelo Géller, la cual guardaremos para perfilar la emergencia de la cerámica en boca.
En la limitación de los muñones, microscópicamente tenemos que meternos un poco por debajo de la terminación marginal para que la lectura del escáner termine justo en esta zona. Si hay que paralelizar alguna zona, la pintaremos en blanco ya que el lector no escanea zonas oscuras y deforma las zonas brillantes (esto es muy importante para el ajuste final).
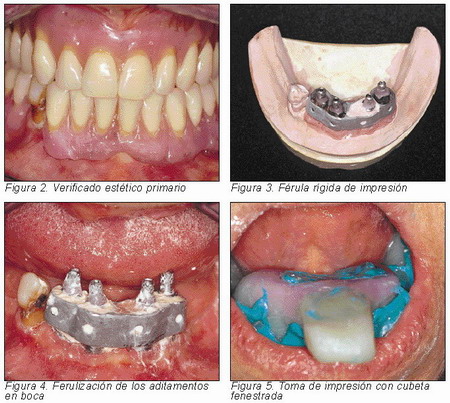
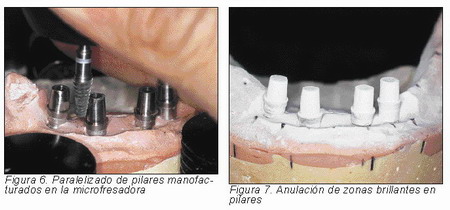
Procedimientos técnicos
Comenzaremos con la orden de trabajo en el ordenador eligiendo el tipo de fresado que vamos a realizar: zirconio y titanio.
Señalaremos en la arcada las piezas o pilares que queremos diseñar y meteremos en el escáner el modelo completo. Seguidamente el ordenador nos pedirá los muñones o pilares de la estructura, colocando por defecto las cofias en los muñones o pilares correspondientes. Este proceso es totalmente mecánico, con lo cual podremos minimizar la pantalla y seguir trabajando en otro diseño (para hacer coronas individuales no hace falta escanear el modelo).
Escaneado el trabajo, por defecto nos llevará al eje de inserción de los pilares, donde la máquina busca automáticamente el más correcto paralelismo de los pilares o muñones (esta opción es manipulable, ya que podemos cambiar el eje de inserción a nuestro gusto).
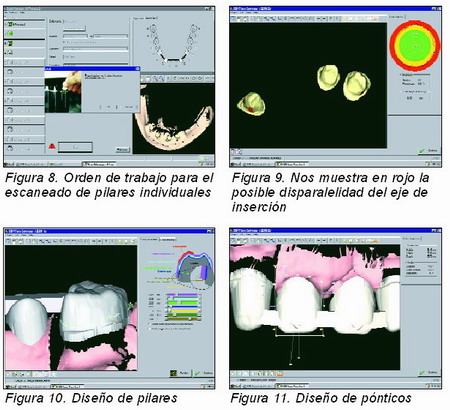
Diseño
El software nos pone automáticamente las piezas pónticas por defecto que hemos elegido en la orden de trabajo. Nosotros ahora jugaremos personalizando los diseños a nuestro gusto.
— Pilares: Aquí elegiremos el espesor del material, dónde queremos añadir el cemento, en qué longitud del pilar queremos friccionar el material, la pintura que queremos dar y el diseño de la terminación cervical.
— Pónticos: Aquí diseñaremos su perfil emergente, longitud, anchura y diámetro a través de los tiradores de diseño.
— Conectores: Es muy importante controlar el espesor, situado en el margen derecho de la orden de trabajo.
En el caso de la híbrida, gracias al nuevo software que nos permite escanear el encerado de la estructura (was-up), es muy importante diseñar cada poste o pilar de retención justo en la zona exacta de donde va a ir posicionada cada pieza.
El escáner DCS está capacitado para medir ópticamente y con precisión 14 muñones individuales con sus pónticas inclusive con un único paso de trabajo. El láser mide 300.000 puntos de la superficie del muñón por minuto con una altísima resolución. Esta potencia garantiza una óptima precisión de la fresadora.
Estudios realizados por diversas universidades han constatado una exactitud de ajuste con espacio marginar menor de 50 um.
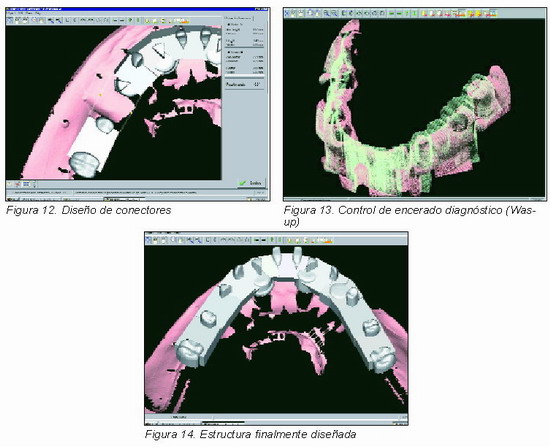
Fresado
Diseñados los trabajos, los lanzaremos por e-mail a cualquier centro de fresado del mundo (DCS Precimill), o en este caso a nuestro propio centro de fresado, digitalizando automáticamente las trayectorias de cada fresa, y así interpretará en qué tipo de material irán los diseños.
En el monitor de la fresadora elegiremos los trabajos que se fresarán, distribuyéndolos en las placas digitales y posicionando las placas reales en la fresadora.
Las fresas que se utilizan para el zirconio son cuatro diamantadas y las utilizadas para titanio son también cuatro de tusteno.
Esta combinación de fresas (todas de distintos diámetros) es muy importante para un buen ajuste coronal.
El proceso de cambio de fresas es totalmente automático, gracias a un gran portafresas situado en la máquina fresadora, pudiendo combinar distintos tipos de materiales en el mismo tiempo de fresado, ya que disponemos de espacio para poder colocar dos placas distintas.
La media de piezas que se pueden llegar a fresar en una placa de titanio son 16; en las cuales invierte un tiempo aproximado de 30 minutos por pieza. En una placa de zirconio la media de piezas fresadas son 11 y el tiempo invertido aproximado es de 3 horas por pieza.
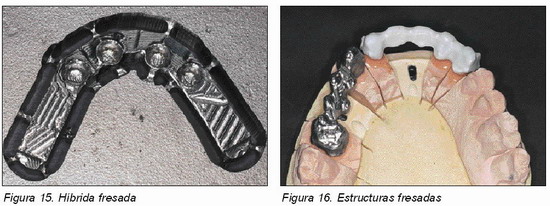
Ajuste
Una vez fresados los trabajos, cortamos los conectores del diseño. En zirconio, los vamos seccionando con una turbina irrigada con agua y una fresa de diamante. En titanio, cortamos con un micromotor convencional entre 15.000 y 20.000 revoluciones con una fresa de tusteno preparada para titanio.
Una vez fresados estos materiales, verificaremos el espesor realizado anteriormente en el diseño (0,5 micras).
Posicionada la estructura en el modelo original, independizaremos las zonas de los contactos por basal, los conectores de la placa y ajustaremos el perfil del margen cervical. Para conseguir una continuidad con la preparación marginal utilizaremos gomas abrasivas de cerámica.
En el diseño implantosoportado fenestraremos la zona incisal de los pilares para poder insertar posteriormente los tornillos. Una vez posicionada la estructura sobre los pilares daremos un punto de soldadura láser en la zona incisal y otro en la zona cervical para la estabilización y el control del ajuste pasivo en boca. (Haremos el montaje de dientes desmontable y una vez verificado el ajuste pasivo en boca, aprovecharemos su posicionamiento para el control estético.)
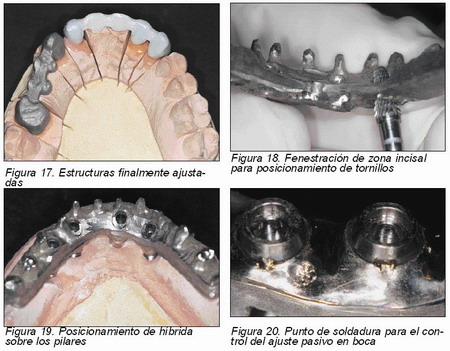
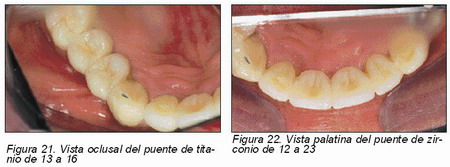
Cerámica
Arenamos las estructuras tanto de zirconio como de titanio con óxido de aluminio entre 110 y 125 micras a 2 bares de presión, con una distancia aproximada para no sobrecalentar la estructura y la vaporizamos.
En el caso de titanio hacemos una pasivización de 20 minutos, después la metemos en el ultrasonido con alcohol isopoprílico durante 5 minutos y volvemos a pasivizar la estructura durante 15 minutos.
Nuestro mejor consejo para trabajar el encubrimiento del zirconio (liner) y del titanio (bonding) es utilizar un aerógrafo (sprayon). Con esto conseguimos una mayor homogeneidad eliminando el oxígeno de la estructura mucho mejor que con un pincel convencional; dejando un mejor encubrimiento uniforme y adhesión de la estructura.
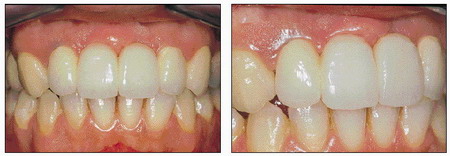
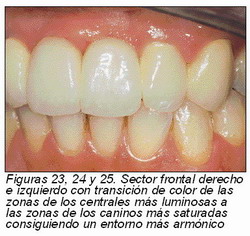
Zirconio
Podemos estratificar nuestros diseños con la cerámica Veneering Ceramic D, en un futuro mejorada con el nombre V.M.9 de la casa Vita, con un coeficiente de expansión de 25-500 ºC y con una resistencia a la rotura de 86 Mpa. Esta cerámica cuece a una temperatura media entre 910 ºC y 940 ºC. O con la cerámica Cercon-Ceram S de la casa DeguDent, con un coeficiente de expansión de 25-600 ºC y una resistencia a la rotura entre 90 y 105 Mpa., obteniendo muy buenos resultados; teniendo posibilidades de jugar con las dentinas 3D y las Flu-Dentin para dar mayor realidad a nuestros trabajos desde el interior. Esta cerámica cuece a una temperatura media entre 825 ºC y 830 ºC.
Gracias al Liner de estas cerámicas conseguimos eliminar la blancura del zirconio consiguiendo la transmisión de luz dentinaria con el color base del paciente.
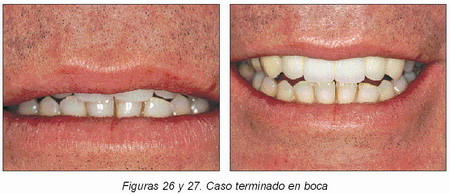
Titanio
Podemos estratificar nuestros diseños con varias cerámicas de baja fusión, por debajo del punto de transformación cristalina (800 ºC).
Trabajamos las cerámicas de nueva generación como Triceram de la casa Dentaurum, con un coeficiente de expansión de 25-400 ºC y una resistencia a la rotura de 50 Mpa. Proporcionándonos una buena estética (válida para la estratificación de otros tipos de materiales muy estéticos como el Cristall), y la cerámica Tikron de la casa Titec, con un coeficiente de expansión de 25-500 ºC y una resistencia a la rotura entre 60 y 100 Mpa. Esta última cerámica, con respecto a las demás tiene una ventaja: la adhesión química del bonder está incluido en el opáquer; y si esto lo unimos al sprayon conseguiremos la fusión químicamente perfecta que siempre hemos soñado con respecto al titanio. Además tiene una menor contracción, la cual es perfecta para personalizar el diseño de los pilares ceramizables.
Una vez preparada la estructura, damos una coción de dentina opaca cubriendo todo el puente para conseguir una profundidad desde el color interior, dando varios cortes en las zonas de los conectores y pónticos para controlar la contracción. Hecho todo esto ya podemos estratificar el diseño del puente a nuestro gusto con todas las referencias correspondientes que hayamos tomado en la sala del color del laboratorio (tintes, saturados, luminosos, opalescentes o traslúcidos). Dependiendo si el paciente viene a tomar el color al laboratorio, haremos una corona estandarizada o la personalizaremos con el paciente en la sala de color.
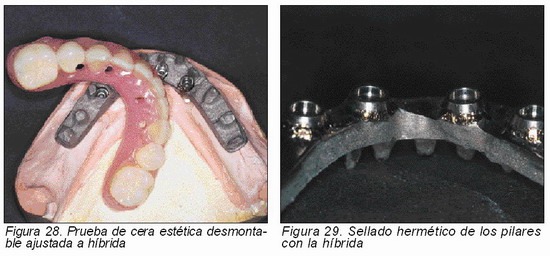
Desarrollo implantosoportado
Comprobado el ajuste pasivo en boca y el control estético haremos un sellado hermético del contorno incisal y cervical con soldadura láser (sin aportar material), puesto que tenemos un ajuste perfecto entre el pilar manofacturado y la estructura fresada.
Alisaremos y puliremos el contorneado basal y chorrearemos la híbrida por las zonas vestibular, lingual y oclusal siguiendo el mismo proceso que con cualquier estructura para prótesis fija.
Una vez pasivizada la estructura la silanizaremos y la dejaremos preparada para la unión química con el opáquer, colocando los dientes en el frente (Creapearl de Willi Geller).
Posicionando el frente, continuaremos con el cargado de resina convencional.
Repasado el diseño de resina, chorrearemos con óxido de aluminio todo su contorno para la individualización del diseño en boca, personalizándola con Lightpaint-on (de la casa Dreve), desarrollada por Klaus Müterthies.
Información clínica
La preparación coronal suele ser convencional con un ángulo cónico entre 5º y 15º en función a la longitud de la pieza.
Para un ajuste preciso y un buen asentamiento de la prótesis necesitamos un hombro entre 90º y 120º.
El cemento se ubicará en la orden del diseño según nos indique el odontólogo. Se puede utilizar cualquier cemento de fosfato de zinc, ionómeros de vidrio o composite polimerizable.
El zirconio sólo se disuelve en ácido fluorídrico, los demás ácidos no le afectan, ni siquiera los álcalis.
En la elaboración de las híbridas disminuiremos el proceso de trabajo ya que se reducen el número de pruebas. Habiendo hecho la prueba estética para la confección de la híbrida, conseguimos un modelo exacto de los implantes en boca con un ajuste pasivo perfecto (F.R.I.); probamos la híbrida para verificar el ajuste pasivo y al mismo tiempo hacemos un montaje de dientes desmontable sobre ésta para la prueba estética final.
Con todo ello disminuiremos tiempo y coste evitando posibles cambios fisico-químicos por una mala manipulación de colado.
Conclusiones
Hoy en día podemos plantearnos el desarrollo de todo tipo de estructuras con ajuste pasivo utilizando el titanio como metal, aprovechando sus excelentes propiedades, consiguiendo un perfecto asentamiento de la superficie del cilindro, combinando los componentes prefabricados o manofacturados con la soldadura láser y el diseño de estructuras fresadas en Cad-Cam; evitando los posibles cambios en las propiedades físico-químicas del titanio por una mala manipulación y estratificando los diseños con cerámicas de nueva generación consiguiendo una estética correcta.
Estamos ante la posibilidad de realizar diseños de fresados curvos de más de un póntico en un material blanco de alta dureza, imposible de colar, con ajustes precisos y químicamente inerte. Sin duda, como lo calificó Ron Garvie, “ACERO CERÁMICO”, material del siglo XXI.
Agradecimientos
Gracias al doctor Gabriel García García (Clínica Argensola) y al doctor Francisco Martínez Celorrio (Clínica Stoma) por su gran colaboración e información fotográfica y clínica recibida; por su formación clínica de mi trayectoía profesional como técnico de laboratorio; por su gran convencimiento sobre la teoría de este proyecto antes del desarrollo final; a su esfuerzo incondicional por dejarme investigar otros tipos de materiales, compartiendo inquietudes comunes y así conseguir lograr una plena satisfacción de nuestro cliente final: el paciente.
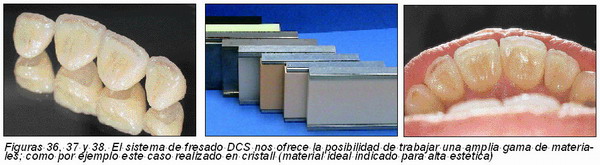
Gracias al esfuerzo incondicional de mi gran equipo al cual estoy orgulloso de pertenecer, equipo joven e inquieto con una mentalidad futura: Yolanda García, Enrique Jiménez, Raúl Martín, Juan Antonio Aranda y Margarita Maldonado (Centro de fresado Ortodentis).
Gracias al doctor Christian y al técnico Joaquín García Domingo por el principio de todo.
Correspondencia
Joaquín García Arranz
C/ Sierra de la Pedriza, 4, posterior.
28923 Alcorcón (Madrid)
Tel.: 916123464
Fax: 914880420
ortodentis@telefónica.net
www.ortodentis.es v
Bibliografía
1. Bredenstein J, Melle. Construcción de un Puente DC-Tell con recubrimiento de composite. Labor Dental Técnica. Vol. 4, n.º5, mayo 2001.
2. Ahlmann D. Ocho años de experiencia con el sistema de fresado DCS. Quintessence Técnica. Marzo 2001. Vol.1 2,-n.º 3.
3. Kappert HF, Gläser R. Una novedosa combinación de materiales para la confección de coronas y puentes mediante la técnica CAD-CAM. Quintessence Técnica. Octubre 1998. Vol. 9, n.º 8.
4. Natt G, Marx R, Spiekermann H, Tinschert J. Metallfreie Fontzahnbrücken aus Holchleistungenskeramik. Dental Labor XLVII, hefl 6/99.
5. Mehl A, Gloger W, Hickel R. Posibilidades del Nuevo sistema de exploración PRECISAN para la tecnología CAD-CAM. Quintessence técnica. Vol. 10 Nº8- octubre 1999.
6. Moreno Martínez J, Iglesia Puig MA. DCS y DC-ZIRCON, una alternativa restauradora estética. Labor Dental (Cerámicas dentales). Abril 2002.
7. Bünemann J, Cléber, Smart. Cercon Smart Ceramics. Labor Dental Técnica. Vol. 4, n.º 5, diciembre 2001.
8. García Arranz J. La fusión del arte y la tecnología en el resultado final: ZIRCONIO / CRISTALL. Labor Dental Técnica. Vol. 5, n.º 6, junio-julio 2002.
9. Moreno Martínez J, Iglesia Puig MA. Titanio colado o fresado y soldadura láser para confección de prótesis híbridas atornilladas sobre implantes. Edicción especial Labor Dental: Las prótesis implantosoportadas en la actualidad.