N. Morenza. CREB. Centro de Investigaciones en Ingeniería Biomédica. / O. Fernández. Dept. Ciencia de los Materiales e Ingeniería Metalúrgica. ETSEIB. Universidad Politécnica de Cataluña / F.J. Gil. Laboratorios Protésicos Fernández. Barcelona
Resumen
En este trabajo se realiza un estudio comparativo de tres metales utilizados ampliamente en la prótesis odontológica: el titanio y las aleaciones Cr-Co y Cr-Ni.
Se comparan sus microestructuras obtenidas mediante fusión y colado, sus propiedades mecánicas: dureza y resistencia a la flexión, la soldabilidad de las aleaciones mediante láser, comparando los valores de resistencia a flexión en uniones soldadas entre el mismo material o bien entre diferentes materiales. Asimismo, se estudia la resistencia a la corrosión y la liberación de iones metálicos al medio salivar.
1. Introducción
Los materiales metálicos utilizados en aplicaciones médicas eran fundamentalmente el oro y la plata hasta el siglo XVIII, posteriormente empezaron a utilizarse los aceros y ya en este siglo aparecieron los aceros inoxidables y las aleaciones de cromo-cobalto-molibdeno, siendo en la década de los 40, cuando se introdujeron el titanio y sus aleaciones en el campo de la medicina. Muchos metales pueden ser tolerados por el cuerpo humano en pequeñas cantidades, (Fe, Cr, Co, Ni, Ti, Ta, Mo, W) y en algunos casos son esenciales, como el caso del hierro en la hemoglobina, cuya misión es el transporte del oxígeno a los tejidos.
Para la buena aplicación de los materiales metálicos deben estudiarse las propiedades mecánicas, si el fin de estos materiales es en parte estructural, así como la resistencia a la corrosión y liberación de iones para su buen comportamiento a largo plazo. Además de la aceptabilidad biológica de los mismos por parte de los tejidos.
En prótesis odontológica también será importante la propiedad de la soldabilidad y en especial la técnica más actual en la prótesis dental que es la soldadura láser. La unión mediante soldadura tiene aplicaciones en odontología en unión de piezas que forman una prótesis única pero que se fabrican por separado a fin de poder ajustarlas con más facilidad. Una vez ajustada cada pieza en el modelo se sueldan con láser y se obtiene la pieza final. Este proceso es conocido con el nombre de ferulizar. También tiene aplicaciones en reparación de pequeñas partes rotas sobre todo en prótesis parciales removibles.
2. Materiales y metodología experimental
2.1. Materiales
Las composiciones químicas y las características nominales de las aleaciones Co-Cr y Ni-Cr utilizadas, se muestran en las Tablas 1 y 2.
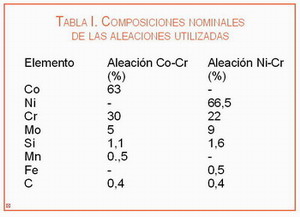
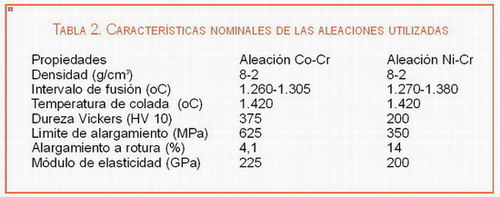
2.2. Obtención de aleaciones: colada para el centrifugado del Co-Cr y del Ni-Cr
Se obtuvieron las aleaciones mediante proceso de fusión por inducción eléctrica. El equipamiento está formado por una cámara cerrada y un brazo rotativo articulado al centro. En un extremo del brazo hay un habitáculo donde se introducen en las posiciones adecuadas el recipiente de la materia prima a fondo y el molde (Figura 1).
Las pastillas de materia prima de composiciones químicas citadas en la Tabla 1, se introducen en el recipiente de la Figura 2, el cual se coloca en su misma posición en el interior del habitáculo del brazo de la máquina de centrifugar. Se coloca también el molde obtenido por revestimiento del modelo en cera en su misma posición.
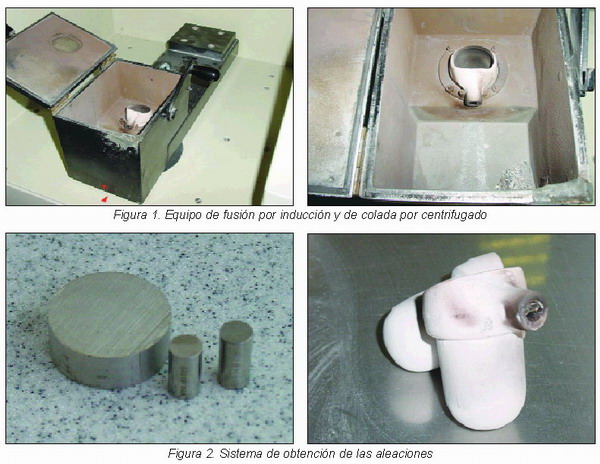
Se cierra el habitáculo y se cierra la cámara. Al comenzar el proceso, en primer lugar la aleación se funde a 1.350-1.450ºC por inducción eléctrica y entonces, por fuerza centrífuga generada por la rotación del brazo articulado, el metal fundido es expulsado radialmente e introducido al molde a presión a través de la entrada cónica y de los canales de distribución. El Ni-Cr necesita más tiempo para fundirse. Todo el proceso tiene una duración de 1-2 minutos. Después de la colada del metal, el conjunto molde-pieza metálica se deja enfriar a temperatura ambiente entre 15 y 20 minutos. Después se procede a la destrucción del molde cerámico con un martillo, obteniendo la pieza final de metal.
Se realizó un molde compuesto de cinco probetas y sus cinco canales de distribución y zonas de alimentación, obteniéndose la pieza final correspondiente. Para obtener cada una de las probetas se cortan con un disco cerámico de corte para metales preciosos y semipreciosos, de manera que tenemos las cinco probetas por un lado, y todos los canales para el colado por otro (Figura 3).
Como control de calidad y para asegurarnos de que los materiales a ensayar presentan condiciones metalográficas idénticas (ausencia de poros y de inclusiones…) se realizaron radiografías con control densitométrico de las piezas. Se ha dispuesto de un equipo radiográfico para laboratorio dental, Cube X Orotig.
2.3. Obtención del titanio
Para las probetas de titanio, se ha utilizado titanio puro, grado 2. El titanio es un elemento muy reactivo con el oxígeno a elevada temperatura. Es por eso que no se puede colar con los otros materiales, en maquinarias ordinarias. La colada de titanio se ha de llevar a cabo en equipos que funcionan bajo cero. Se ha dispuesto de un equipo de vacío para colar titanio, Titec-Orotig. Una vez obtenido el molde con un revestimiento especial, éste se introduce en la cámara de colada con la entrada cónica a la parte superior, orientada al orificio que conecta con la cámara de fusión. El molde queda fijado por el plato neumático. Un segundo mando neumático hace girar la configuración de las cámaras desde la posición vertical hasta la horizontal. Se coloca entonces la pastilla de titanio sobre el crisol de cobre de la cámara de fusión, bajo el electrodo de tungsteno que genera el arco. Se realizan los controles de las probetas mediante sistema radiográfico.
2.4 Técnicas de caracterización microestructural
Para la caracterización de los materiales, se han llevado a cabo preparaciones diferentes según las técnicas a utilizar.
2.4.1. Microscopía óptica
En primer lugar se han cortado dos muestras de cada aleación, Co-Cr y Ni-Cr, una de las pastillas de materia prima, y otra de las piezas obtenidas por colada en el laboratorio. Las muestras se han colocado en baquelita y entonces se han desbastado, con papeles de 400, 600 y 1.200 mm, y después se han pulido a 1 y 0,05 mm con alúmina. Después del pulido se atacaron químicamente. El Co-Cr y Ni-Cr se han atacado en agua regia (4 partes HCl, una parte HNO3), sumergiendo y sacando la muestra repetidas veces hasta observar una superficie mate. En el caso del Ti, se atacaron con reactivo de Kroll (5% HF, 10% HNO3, 85% H2O), sumergiendo la muestra durante 15 segundos.
2.5. Técnicas de caracterización mecánica
En la caracterización del Co-Cr, del Ni-Cr y del Ti se han hecho ensayos de flexión por tres puntos en ensayos de dureza mediante indentación Vickers para determinar la resistencia y la dureza de estos materiales.
2.5.1. Flexión por tres puntos
Las propiedades mecánicas de los materiales utilizados en odontología, concretamente en prótesis parciales removibles, se determinan normalmente a partir de ensayos de flexión, ya que estos tipos de deformación se considera que es más representativa de las condiciones clínicas que los ensayos de tensión convencionales utilizados en materiales metálicos. En estos estudios se han realizado ensayos por tres puntos en probetas de sección cuadrada. La determinación de las dimensiones de las probetas se tomó considerando que fuesen una aproximación de la realidad, pero sin ser demasiado pequeñas como para poder ensayarlas en los equipos convencionales. En caso de probetas demasiado pequeñas, podrían producirse interacciones no deseadas. La geometría de las probetas es la de la Figura 4.
Los ensayos de flexión por tres puntos, se han llevado a cabo en un equipo de tracción Instron con unas mordazas adecuadas. En la Figura 5 se muestra el tipo de ensayo realizado.
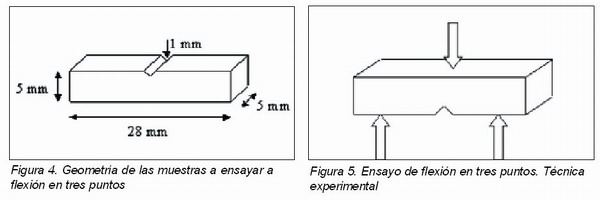
2.5.2. Dureza
El método de determinación consiste en hacer penetrar bajo una cierta presión un determinado cuerpo (penetrador) dentro del material a estudiar, e identificar después la penetración, la profundidad del empuje. La dureza es entonces una propiedad sobre todo de superficie. Se han hecho ensayos de microdureza con indentador Vickers con un microdurómetro Matsuzawa con una carga aplicada de 500 g. durante 15 segundos, sobre las superficies pulidas.
2.6. Soldadura
El equipo de soldadura del que se ha dispuesto es un láser dental “Flash 2000” que está formado por un láser de polos de alta energía (cristal de láser Nd. YAG), una cámara de trabajo con clase de protección de láser 4, alimentación doble de gas protector en toda la pieza de trabajo. Este equipo proporciona un rayo láser de diámetro muy pequeño, que es el que interesa en aplicaciones dentales donde se realizan trabajos de precisión, pero que representa un inconveniente para las soldaduras de probetas de dimensiones relativamente grandes, teniendo en cuenta que no se pueden soldar superficies de ciertas dimensiones.
Para una correcta soldadura, se ha tenido que mecanizar la superficie a soldar en forma de punta, de manera que haya un contacto puntual entre las dos partes a soldar y el equipo pueda hacer la soldadura. A partir de aquí, si se desea, con material de aportación se puede aumentar la superficie soldada. Se han mecanizado las probetas con un disco cerámico de una forma piramidal de base cuadrada. Se ha procedido entonces a hacer la soldadura. Los componentes a soldarse se unen manualmente bajo control visual en el interior de la cámara de trabajo, de manera que estén en contacto puntual según el mecanizado, y se suelden mediante uno o unos cuantos impulsos de láser. Se hace un primer punto de soldadura de manera que las dos partes queden unidas, y a partir de aquí con más impulsos de láser se va aumentando la superficie soldada. Si se prefiere también se puede soldar con material de aportación e ir ampliando el espacio vacío del mecanizado (Figura 6).
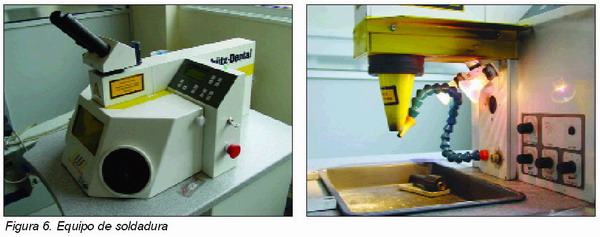
Los parámetros de control, son el voltaje de la lámpara, la duración del impulso, la división de los polos y la frecuencia de sucesión de polos automática. Las soldaduras se han numerado con una letra y con dos números correspondientes a los números de las probetas iniciales de las cuales procedían (Tabla 3).
Para la observación de las operaciones de fractura, se ha utilizado un microscopio electrónico de barrido, utilizando un modelo JEOL 6400 con microanálisis de energía dispersiva de Rayos X Lynk.
2.7. Técnicas de caracterización química
2.7.1. Liberación de iones
Se realizaron estudios de liberación de iones de las aleaciones Co-Cr y Ni-Cr al medio salivar a diferentes tiempos de experimentación para una misma superficie. El medio salivar artificial se muestra en la Tabla 4, que es el utilizado comúnmente. Se extrajeron 10 ml de líquido de cada uno de los recipientes que contenían las aleaciones de Co-Cr y Ni-Cr. Las muestras fueron tomadas al cabo de 1 hora, 2, 3, 5, 8,5, 1 día 2, 3, 6, 10, y 17 días. Las concentraciones de iones liberados se estudiaron mediante un equipo de análisis de espectroscopía de masas con plasma inducido (ICP-MS).
2.7.2. Corrosión electroquímica
Para el estudio de la corrosión que padecen los materiales, se va a seleccionar una muestra de cada de una de las dimensiones adecuadas, con una superficie de unos 0,15 cm2. Se desbasta una de las superficies y después se pule hasta 0,1 mm. En un recipiente con solución fisiológica Hank’s se va a colocar un electrodo de platino y otro de plata-cloruro de plata y la muestra de Cr-Ni y Cr-Co embaquelitada. El recipiente se va a poner en un baño de agua destilada a 37 ºC y se conectan los electrodos y la muestra. Entre el electrodo de plata-cloruro de plata y la muestra se establece un potencial, y el de platino es el de referencia. Se utiliza un potenciosta Voltalab Master. En primer lugar se va a esperar 3 horas a que el potencial libre se estabilice y después se hace un barrido de potencial, desde -1,5 hasta a + 2 V y se determina la resistencia a la corrosión.
3. Resultados experimentales y discusión
3.1. Microestructuras observadas
Las microestructuras de Co-Cr obtenidas (Figura 7) presentan dendritas de solidificación orientadas hacia el centro, lo cual nos indica la dirección de eliminación del calor. Se puede apreciar que hay dos fases, correspondiente a la fase e con segregación rica en cromo que puede llegar a formar la fase s de la aleación Co-Cr. Para mejorar la solubilidad y por tanto la homogeneidad de la aleación, se debería enfriar más lentamente durante el proceso de solidificación con el fin de seguir las condiciones de equilibrio termodinámico o bien calentar la aleación sólida a una temperatura de 800-900 ºC para producir la difusión en estado sólido por vacantes (solución sólida sustitucional).
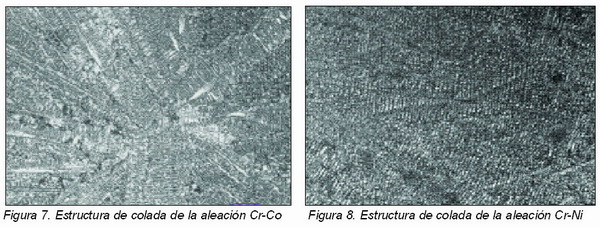
Esta homogeneización proporcionará una mejora en la resistencia a la corrosión del material colado y hará una liberación de tensiones residuales de solidificación más grande, además de conseguir una respuesta física y mecánica más predecible de la aleación.
La microestructura del Ni-Cr es muy similar a la del Co-Cr ya que los elementos de aleación respecto al cromo se asemejan mucho y por tanto el comportamiento en la solidificación es también muy similar. En cambio, al tener una conductividad calorífica diferente, la aleación Ni-Cr libera de manera no direccional el calor y por tanto se puede observar una pérdida de direccionalidad de las dentritas formadas. La solución sólida que se forma en el Ni-Cr es la fase a y las segregaciones de cromo producen la aparición de la fase g. Las dendritas son más largas y más finas que en el caso del Co-Cr debido a que esta aleación tiene un proceso de crecimiento del cristal favorable y tiene una mayor energía motriz para que el sólido asuma la distancia de mínimo subenfriamiento (Figura 8).
Las segregaciones obtenidas en las dos aleaciones son debidas, según se ha comentado, a la rápida velocidad de solidificación o al menos a la no consecución de velocidades de solidificación suficientemente lentas como para conseguir las condiciones de equilibrio y la perfecta homogeneización de las soluciones sólidas.
La microestructura del titanio puro comercializado se puede observar en la Figura 9. Está formada por grandes equiaxiales (120º) que no presentan ninguna direccionalidad concreta de la fase a. Esta es hexagonal y presenta una gran anisotropía. Se puede observar en el interior de las grandes maclas de defectos de apilamiento pero no son debidas a procesos de deformación. Al ser un metal puro no hay segregaciones químicas y por tanto tendrá un buen comportamiento ante la corrosión.
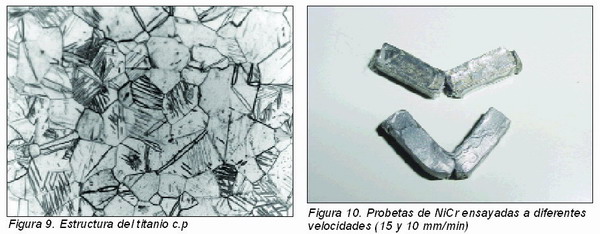
3.2. Caracterización mecánica
3.2.1. Resistencia a la flexión en tres puntos
Las probetas obtenidas por moldeo a la cera perdida en los laboratorios dentales, se han ensayado en una máquina de flexión por tres puntos. Se hacen unos primeros ensayos con probetas Ni-Cr con una velocidad de desplazamiento de las mordazas de 10 mm/min. Esta velocidad no era adecuada por que las probetas se deformaban mucho antes de romperse, y presentaban una rotura excesivamente dúctil. Se fabricaron cinco probetas más de Ni-Cr y se ensayaron a 15 mm/min, considerándose ésta como la velocidad de ensayo, con roturas más frágiles (Figura 10).
A partir de las gráficas carga-deformación se han obtenido los valores de la Tabla 5. Se pueden ver claras diferencias entre los tres materiales. El Co-Cr y el Ni-Cr presentan valores máximos de carga similares (alrededor de los 4 kN), pero unos valores de deformación muy diferentes (Co-Cr, flecha 1-2 mm) respecto al Ni-Cr que se deforma mucho más (flecha superior a 6 mm). El Ni-Cr absorbe mucha más energía a la rotura y por tanto presenta mayor tenacidad que el Cr-Co. Por lo que respecta al Ti, éste representa valores máximos de carga inferiores a las aleaciones (2,75 kN, y unas deformaciones intermedias entre los otros dos materiales.
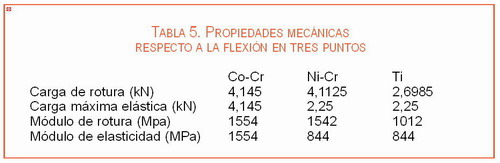
En caso de utilizar la carga de rotura se obtiene el módulo de rotura, y en caso de utilizar la carga máxima en régimen lineal se obtiene el que se podría denominar módulo de elasticidad. Estos parámetros, como ya se ha comentado, nos sirven para comparar entre los diferentes materiales. Los valores numéricos obtenidos por los diferentes materiales se presentan en la Tabla 5.
3.2.2. Dureza
Los ensayos de dureza realizados a las tres muestras han dado los valores de la Tabla 6. Se puede observar que la aleación Cr-Co es la de mayor dureza, seguida por el titanio y por la aleación Cr-Ni. Por tanto, la aleación Cr-Ni será la que tendrá un peor comportamiento a desgaste de las tres.
3.2.3. Resistencia a flexión de soldaduras
Durante el proceso de soldadura fue posible ver cómo la soldadura del Ti con el Co-Cr y el Ni-Cr era prácticamente imposible. Era una soldadura muy frágil que se rompía al más mínimo movimiento. El resto de probetas soldadas se van a ensayar en flexión por tres puntos, cuyos resultados se reflejan en la Tabla 7.
Se puede observar cómo las soldaduras de Ni-Cr con Ni-Cr y de Ti con Ti son muy resistentes tanto con material de aportación como sin él y en cambio la soldadura de Co-Cr con Co-Cr que se va llevar a cabo sin material de aportación es muy poco resistente.
3.2.4. Superficies de fractura
Se realizó un estudio fractográfico de las muestras ensayadas observando la mayor ductilidad de la aleación Cr-Ni respecto a la de Titanio y Cr-Co. En la Figura 12 puede observarse el mayor daño en la superficie de la aleación Cr-Ni, lo que señala su gran tenacidad a la fractura.
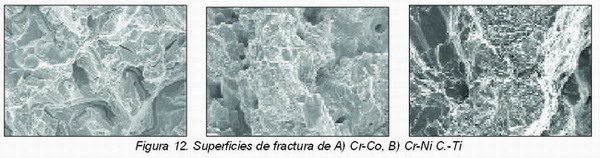
3.3. Caracterización química
3.3.1. Liberación de iones
En la Figura 13 se muestra cuál es la evolución de los iones de Co y de Ni liberados al medio por cada muestra. Se observa claramente cómo el Ni-Cr libera más iones (cuatro veces más) que el Co-Cr. Estos iones liberados son los que pueden provocar problemas alergogénicos asociados al níquel.
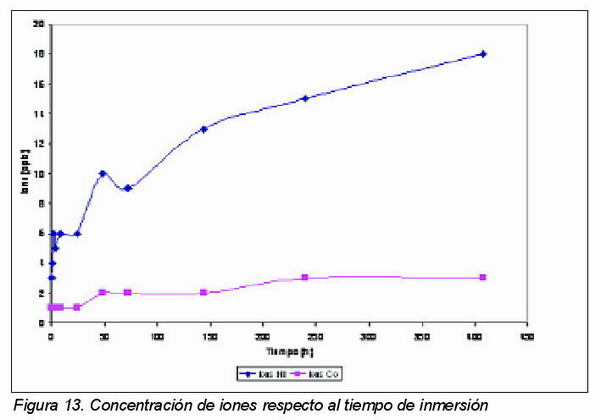
3.3.2. Corrosión
Se hizo el ensayo de corrosión con una muestra de Co-Cr y otra de Ni-Cr. Las superficies eran de unos 0,20 cm2. Después de preparar las muestras y el dispositivo se va hacer una estabilización del potencial libre de tres horas, tiempo que en ninguno de los dos casos no va a ser del todo suficiente para conseguir una buena estabilización. Se va a proceder entonces a hacer la limpieza de potencial. Se va a poder observar cómo sobre los 0,6 V se va a producir el rompimiento de la capa, y la corriente va a comenzar a aumentar de forma importante, consiguiendo una corriente máxima de unos 250 mA/cm2. Los materiales presentaban una repasivación bastante rápida, disminuyendo la corriente al aparecer la nueva capa de óxido.
Los materiales van a sufrir la rotura de la capa a un potencial relativamente pequeño respecto al titanio, así que no tienen una resistencia a la corrosión tan buena como el titanio. Por lo que respecta a la comparación entre ellos, en los ensayos únicos hechos en cada material, presentaron un comportamiento prácticamente igual. La rotura de la capa se produjo a 630 mV para el Ni-Cr y 660 mV para el Co-Cr, con cuyo resultado, se puede decir que el Co-Cr es ligeramente más resistente a la corrosión. Por lo que respecta a la repasivación, los dos materiales presentan una gráfico similar, con una anchura de la curva prácticamente igual, así que ambos tienen una repasivación parecida.
Bibliografía
1. Benard, Michel, Philibert, Talbot. Metalurgia general. Editorial Hispano Europea, Barcelona, 1973.
2. O»Brien WJ. Dental Materials. Properties and selection. Quintessence Publishing Co., Chicago, 1989.
3. Bronzino JD. The Biomedical Engineering Handbook. CRC Press/IEEE Press, USA, 1995.
4. Burdairon G. Manual de biomateriales dentarios. Masson, Barcelona, 1991.
5. Combe EC. Materiales dentales. Editorial Labor, Barcelona, 1990.
6. Combe EC. Notes on dental materials. Churchill Livingstone, Singapore, 1992.
7. Craig, O»Brien, Powers. Materiales dentales. Propiedades y manipulación. Mosby, Barcelona, 1996.
8. Macchi. Materiales dentales. Fundamentos para su estudio. Ed. Médica Panamericana, Buenos Aires, 1988.
9. Ryhänen J. Biocompatibility evaluation of nickel-titanium shape memory metal alloy. Acta Universitatis Ouluensis, Oulu University Press, Oulu, 1999.
10. Williams D. (ed.). Concise Encyclopedia of Medical & Dental Materials. Pergamon Press, 1990.
11. Wilson HJ, Mansfield MA, Heath JR, Spence D. Dental Technology and Materials for Students, Blackwell Scientific Publications, 1987.
12. AENOR. Odontología. Materiales dentales. Asociación Española de Normalización y Certificación, Madrid, 1999.
13. ASM Handbook. Vol 2. Properties and selection: nonferrous alloys and special-purpose materials, USA, 1990.
14. ASM Handbook. Vol 3. Alloy Phase Diagrams, ASM International, USA, 1993.